Bionic multi-degree of freedom precise piezoelectric driving device
A piezoelectric drive, degree of freedom technology, applied in the direction of generator/motor, piezoelectric effect/electrostrictive or magnetostrictive motor, electrical components, etc., can solve the phenomenon of creeping, low positioning accuracy, and structural size Large and other problems, to achieve the effect of compact structure, low driving power, and accurate rotary motion
- Summary
- Abstract
- Description
- Claims
- Application Information
AI Technical Summary
Problems solved by technology
Method used
Image
Examples
Embodiment Construction
[0024] The detailed content of the present invention and its specific implementation will be further described below in conjunction with the accompanying drawings.
[0025] see Figure 1 to Figure 8 As shown, the bionic multi-degree-of-freedom precision piezoelectric drive device of the present invention includes two parts, the rotor 1 and the stator 2. The rotor 1 is a rotating shaft, which transitionally fits with the shaft hole in the middle of the stator 2, and its output end has three uniform Distributed threaded holes Ⅰ, Ⅱ, Ⅲ3, 4, 5 are used as power output.
[0026] see Figure 4 , Figure 6 and Figure 7 As shown, the stator 2 is divided into the upper, middle and lower three-layer structure of the stator. The three-layer structure of the stator is connected by thin-walled flexible hinges A and B. The upper layer of the stator and the middle layer of the stator are the rotating drive parts, and the middle layer of the stator and the lower layer of the stator For th...
PUM
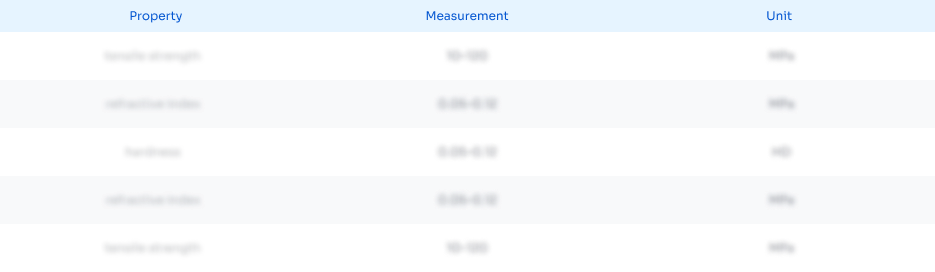
Abstract
Description
Claims
Application Information

- R&D
- Intellectual Property
- Life Sciences
- Materials
- Tech Scout
- Unparalleled Data Quality
- Higher Quality Content
- 60% Fewer Hallucinations
Browse by: Latest US Patents, China's latest patents, Technical Efficacy Thesaurus, Application Domain, Technology Topic, Popular Technical Reports.
© 2025 PatSnap. All rights reserved.Legal|Privacy policy|Modern Slavery Act Transparency Statement|Sitemap|About US| Contact US: help@patsnap.com