Wear-resisting concrete terrace overall molding construction method
A construction method and integral molding technology, applied in the direction of floors, buildings, building structures, etc., can solve the problems of long construction period, cracks and hollows, etc., and achieve the effect of low cost, consistent color tone and high wear resistance
- Summary
- Abstract
- Description
- Claims
- Application Information
AI Technical Summary
Problems solved by technology
Method used
Image
Examples
Embodiment 1
[0021] The construction method of the integral molding of wear-resistant concrete floor according to the present invention comprises the following steps:
[0022] According to the conventional method, the base concrete is poured and tamped in sections. After vibrating, it is repeatedly rolled with a steel roller. After the scraping, the cement slurry floats to a thickness of 4mm, and the excess water is drained with a rubber tube; wait for 35 minutes before using Add a disc to the leveling machine to level the ground and lift the pulp; after lifting the pulp, wait until the feet step on it and sink about 5mm, start spreading 2 / 3 of the wear-resistant material and smooth it with a wooden trowel; wait for the first time The spreaded material absorbs water and becomes evenly darker in color, and the surface seems to be completely black. Use a trowel and a disc to grind and disperse, and then carry out rough grinding and smoothing, and grind it vertically and horizontally for 3 tim...
Embodiment 3
[0027] A specific example of the construction method of the integral molding of the wear-resistant concrete floor of the present invention includes the following steps:
[0028] The concrete wear-resistant floor area of a factory building is 23,000 square meters for trial use. The base concrete is poured and tamped in sections according to the conventional method. After vibration, it is repeatedly rolled with a special steel roller. Use a rubber tube to drain the stagnant water; wait for 45 minutes and then use a trowel and a disc to level the ground and lift the slurry; after lifting the slurry, wait until the foot steps on it, and when it sinks about 5mm, start spreading 2 / 3 of the amount For wear-resistant materials, use a wooden trowel to smooth them; when the material that is spread for the first time absorbs water, the color will become evenly darker, and the surface seems to be completely black. Level 4 times; immediately after spreading the wear-resistant material fo...
PUM
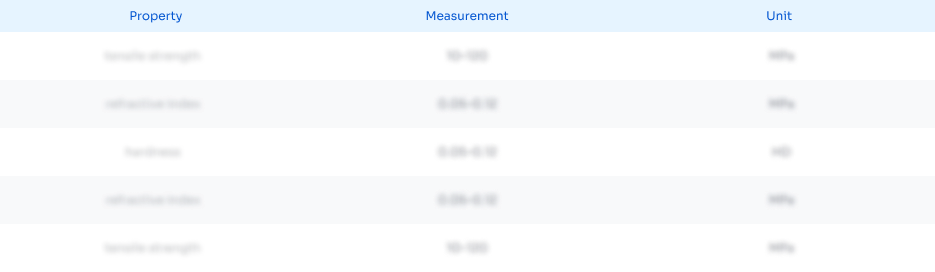
Abstract
Description
Claims
Application Information

- R&D
- Intellectual Property
- Life Sciences
- Materials
- Tech Scout
- Unparalleled Data Quality
- Higher Quality Content
- 60% Fewer Hallucinations
Browse by: Latest US Patents, China's latest patents, Technical Efficacy Thesaurus, Application Domain, Technology Topic, Popular Technical Reports.
© 2025 PatSnap. All rights reserved.Legal|Privacy policy|Modern Slavery Act Transparency Statement|Sitemap|About US| Contact US: help@patsnap.com