Method for accurately controlling trimming line of turned edge under complex curved surface
A technology for flanging and trimming lines and complex surfaces, which is applied in special data processing applications, instruments, electrical and digital data processing, etc. good quality effect
- Summary
- Abstract
- Description
- Claims
- Application Information
AI Technical Summary
Problems solved by technology
Method used
Image
Examples
Embodiment Construction
[0039] The present invention will be further described below in conjunction with the accompanying drawings, but the protection scope of the present invention is not limited to the scope described in the embodiments.
[0040] like figure 1 As shown, the part to be processed is a car door glass guide rail structure, the material is galvanized sheet, the thickness of the material is 1.2mm, and it is used for the electric glass regulator of the car. The door glass guide rail structural part has a complex curved surface; the upper and lower ends of the door glass guide rail structural part are upper flange 1 and lower end flange 2, and the flange edge precision of the door glass guide rail structure requires high precision and the error of some areas is controlled at 0.8 per side within mm. As shown in Fig. 2(a) and Fig. 2(b), the surfaces of the upper end flanging shape 3 and the lower end flanging shape 5 of the door glass guide rail structure are complex curved surfaces combine...
PUM
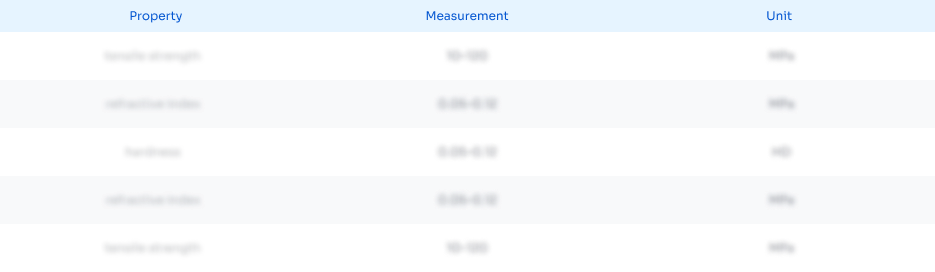
Abstract
Description
Claims
Application Information

- R&D Engineer
- R&D Manager
- IP Professional
- Industry Leading Data Capabilities
- Powerful AI technology
- Patent DNA Extraction
Browse by: Latest US Patents, China's latest patents, Technical Efficacy Thesaurus, Application Domain, Technology Topic, Popular Technical Reports.
© 2024 PatSnap. All rights reserved.Legal|Privacy policy|Modern Slavery Act Transparency Statement|Sitemap|About US| Contact US: help@patsnap.com