High-efficiency environment-friendly ketene dimer production technique
A diketene, production process technology, applied in the field of diketene production, can solve the problems of increasing the processing cost and the pressure of environmental protection, affecting the quality and yield of diketene, and achieving the goal of reducing gas desorption, reducing the generation of polymers, and increasing solubility Effect
- Summary
- Abstract
- Description
- Claims
- Application Information
AI Technical Summary
Problems solved by technology
Method used
Examples
Embodiment 1
[0019] Feeding 2500L / h of acetic acid aqueous solution with a mass concentration of 93% is vaporized into acetic acid gas by the acetic acid vaporizer, and then preheated to 520°C through the acetic acid preheating section. As a catalyst, the catalyst is mixed with acetic acid gas and gasified and enters the cracking furnace together. The temperature of the cracking furnace is controlled at 695°C. The acetic acid gas is cracked in the cracking furnace to produce ketene gas, water vapor and by-products such as carbon monoxide, carbon dioxide, and methane. . The outlet pressure of the cracking furnace is an absolute pressure value of 10KP. The gas exiting the cracking furnace is cooled and separated to remove water vapor and unreacted acetic acid, as well as acetic acid and acetic anhydride produced during the reaction process. The purified ketene gas is transported backward through a vacuum pump. The pre-pump pressure of the vacuum pump is controlled to an absolute pressure val...
Embodiment 2
[0021]Feeding 2000L / h of acetic acid aqueous solution with a mass concentration of 92% is vaporized into acetic acid gas by the acetic acid vaporizer, and then preheated to 560°C through the acetic acid preheating section. As a catalyst, the catalyst is mixed with acetic acid gas and gasified and enters the cracking furnace together. The temperature of the cracking furnace is controlled at 698°C. The acetic acid gas is cracked in the cracking furnace to produce ketene gas, water vapor and by-products such as carbon monoxide, carbon dioxide, and methane. . The outlet pressure of the cracking furnace is an absolute pressure value of 8KP. The gas exiting the cracking furnace is cooled and separated to remove water vapor and unreacted acetic acid, as well as acetic acid and acetic anhydride produced during the reaction process. The purified ketene gas is transported backwards by a vacuum pump. , control the pressure before the pump of the vacuum pump to an absolute pressure value ...
PUM
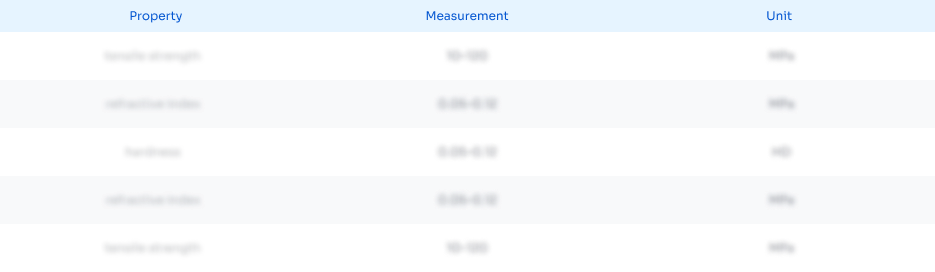
Abstract
Description
Claims
Application Information

- R&D
- Intellectual Property
- Life Sciences
- Materials
- Tech Scout
- Unparalleled Data Quality
- Higher Quality Content
- 60% Fewer Hallucinations
Browse by: Latest US Patents, China's latest patents, Technical Efficacy Thesaurus, Application Domain, Technology Topic, Popular Technical Reports.
© 2025 PatSnap. All rights reserved.Legal|Privacy policy|Modern Slavery Act Transparency Statement|Sitemap|About US| Contact US: help@patsnap.com