Hot rolling mill AGC system and rolling control method thereof
A control method and technology for hot rolling mills, which are applied in rolling mill control devices, rolling force/roll gap control, metal rolling, etc., and can solve the requirements that affect the constant pressure of equipment, poor control accuracy, and low sheet thickness control accuracy, etc. problems, to achieve the effect of high control accuracy and fast response speed
- Summary
- Abstract
- Description
- Claims
- Application Information
AI Technical Summary
Problems solved by technology
Method used
Image
Examples
specific Embodiment approach 1
[0022] Specific implementation mode one: combine figure 1 Describe this embodiment, the AGC system of the hot rolling mill described in this embodiment, the model of the pressure sensor of the AGC system of the hot rolling mill is TIM0050302911201, and the pressure sensor is arranged in the oil cylinder of the AGC system of the hot rolling mill;
[0023] The pressure sensor is a TIM0050302911201 pressure sensor modified according to the set calibration parameters;
[0024] The pressure sensor is used to collect the pressure in the oil cylinder of the AGC system of the hot rolling mill, and feeds back to the hydraulic servo system of the AGC system of the hot rolling mill as a control parameter.
[0025] In this embodiment, the parameter calibration design, positioning control and constant pressure control are carried out again through sensor modification to realize the constant roll gap, constant pressure and differential adjustment functions of the rolling mill, so as to impr...
specific Embodiment approach 2
[0042] Embodiment 2: This embodiment is a further limitation of the hot rolling mill AGC system described in Embodiment 1. The hydraulic servo system of the hot rolling mill AGC system includes a signal processing module, a controller, a servo amplifier, an electro-hydraulic Servo valve, cylinder signal compensation module and switch;
[0043]The displacement feedback signal output end of the displacement sensor of the AGC system of the hot rolling mill is connected to one feedback signal input end of the switch, and the pressure feedback signal output end of the pressure sensor of the AGC system of the hot rolling mill is connected to the other feedback signal input end of the switch. The feedback signal output end of the switch is connected to the first feedback signal input end of the signal processing module; the roll gap control instruction signal output end of the pressing control system is connected to the second feedback signal input end of the signal processing module,...
specific Embodiment approach 3
[0053] Specific embodiment three: this embodiment is the rolling control method of the hot rolling mill AGC system described in specific embodiment one, through the switching of the switching switch, the rolling control method of the hot rolling mill AGC system includes pressure control method and roll gap control method,
[0054] When switching from the pressure control method to the roll gap control method, take the current roll gap as the initial value of the roll gap, and adjust the roll gap pressure until the target roll gap is reached; when switching from the roll gap control method to the pressure control method, use the current The pressure value is used as the initial pressure value, and the pressure is adjusted until the target pressure is reached;
[0055] Both the pressure control method and the roll gap control method adopt the given value of S-shape change for rolling control.
[0056] According to the function of this system is to control the roll gap (thicknes...
PUM
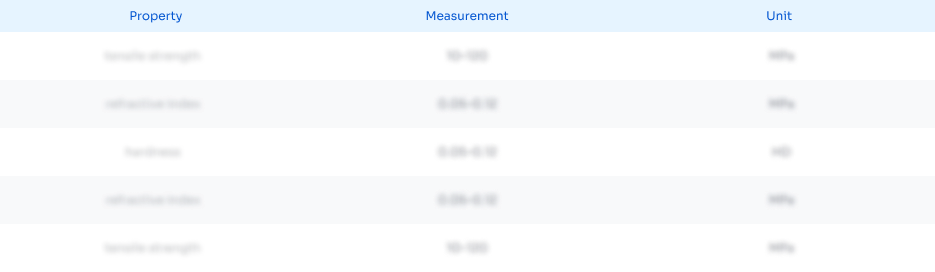
Abstract
Description
Claims
Application Information

- Generate Ideas
- Intellectual Property
- Life Sciences
- Materials
- Tech Scout
- Unparalleled Data Quality
- Higher Quality Content
- 60% Fewer Hallucinations
Browse by: Latest US Patents, China's latest patents, Technical Efficacy Thesaurus, Application Domain, Technology Topic, Popular Technical Reports.
© 2025 PatSnap. All rights reserved.Legal|Privacy policy|Modern Slavery Act Transparency Statement|Sitemap|About US| Contact US: help@patsnap.com