A double-chamber four-station glass bending tempering device and control method
A four-station, glass technology, applied in glass tempering, glass manufacturing equipment, glass production, etc., can solve the problems that the overall temperature of the glass plate is difficult to achieve uniformity, the quality of the glass plate is not ideal, and the heating temperature is high, and the heating time can be achieved. Effects of shortening, avoiding waveforms, and improving surface quality
- Summary
- Abstract
- Description
- Claims
- Application Information
AI Technical Summary
Problems solved by technology
Method used
Image
Examples
Embodiment 1
[0022]The discharge end of the preheating furnace 1 is set correspondingly to the feed end of the heating furnace 2, the feed end of the preheating furnace 1 is provided with the upper section 4, and the bending steel forming section is provided between the discharge end of the heating furnace 2 and the section 5 3. The arc-changing mechanism 3-2 is set in the bending steel forming section 3; above the upper section 4 and the taking section 5, the elevation of the conveying roller 8 in the preheating furnace 1 and the heating furnace 2 is consistent, and the preheating furnace 1 and the heating furnace 2 A temperature control system is set above and below the conveying roller 8. The middle line of the preheating furnace 1 and the feeding end and the discharging end form a heating zone A for one station and a heating zone B for two stations. The middle line of the heating furnace 2 The three-station heating zone C and the four-station heating zone D are formed between the line, ...
Embodiment 2
[0024] The operating sequence of the glass 9 is the upper section 4, the first station heating zone A, the second station heating zone B, the third station heating zone C, the four station heating zone D, the bending steel forming section 3, the taking section 5; the upper section 4 The conveying roller 8 drives the glass 9 to enter the induction zone at the feed end of the preheating furnace 1 and stops to enter, and the conveying roller 8 in the heating zones A, B, C and D of the first, second, third and fourth stations drives the heated glass 9 moves forward at the same time, the glass 9 in the induction area of the feeding end of the preheating furnace 1 enters the heating area A of the first station, and at the same time, the glass 9 is replenished on the upper section 4, and the conveying roller 8 of the heating area D of the four stations drives the glass 9 from the outlet The material end enters the variable arc mechanism 3-2 of the bending steel forming section 3, an...
Embodiment 3
[0026] In the preheating furnace 1, the heating temperature of the heating zone A of the first station is 0-450 degrees, the set temperature of the whole glass 9 is 450-5-450+5 degrees, and the heating temperature of the heating zone B of the second station is 450-490 degrees. The set temperature of the glass 9 is 490-5~490+5 degrees; the heating temperature of the three-station heating zone C in the heating furnace 2 is 490~590 degrees, and the set temperature of the whole glass 9 is 590-5~590+5 degrees. The heating temperature of the station heating zone D is 590-700 degrees, and the set temperature of the whole glass 9 is 700-10-700+10 degrees.
PUM
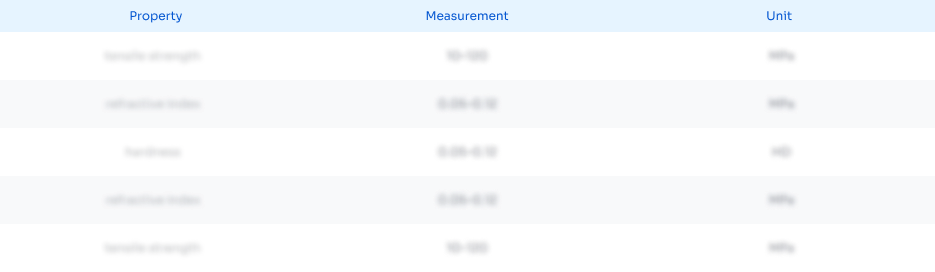
Abstract
Description
Claims
Application Information

- R&D
- Intellectual Property
- Life Sciences
- Materials
- Tech Scout
- Unparalleled Data Quality
- Higher Quality Content
- 60% Fewer Hallucinations
Browse by: Latest US Patents, China's latest patents, Technical Efficacy Thesaurus, Application Domain, Technology Topic, Popular Technical Reports.
© 2025 PatSnap. All rights reserved.Legal|Privacy policy|Modern Slavery Act Transparency Statement|Sitemap|About US| Contact US: help@patsnap.com