A method for preparing high-precision resistance on the surface of an LTCC substrate
A substrate surface, high-precision technology, applied in the direction of resistance manufacturing, resistors, coating resistance materials, etc., can solve the problems of film adhesion, poor electrode solder resistance, low resistance value accuracy, etc., to achieve good solder resistance , high line precision and high application frequency
- Summary
- Abstract
- Description
- Claims
- Application Information
AI Technical Summary
Problems solved by technology
Method used
Examples
Embodiment Construction
[0036] A method for preparing high-precision resistance on the surface of a LTCC substrate is specifically implemented as follows:
[0037] (1) Prepare a multilayer LTCC substrate, grind and polish the surface of the LTCC substrate with a grinder and a polishing machine;
[0038] (2) Soak the LTCC substrate treated in step (1) with acetone for 3 times, the total soaking time is not less than 30min, and ultrasonic treatment is performed in the first and last 1min to 3min of the first soaking process; the second and third soaking process Ultrasonic treatment is carried out in the last 1min to 3min of the process; the LTCC substrate is taken out from the acetone, and then immersed in ethanol for 2 times, the total soaking time is not less than 10min, and ultrasonic treatment is performed in the first 1min of each soaking process; Take it out, spray and clean it with deionized water; dry the LTCC substrate with nitrogen; place the LTCC substrate on a hot plate for drying;
[0039...
PUM
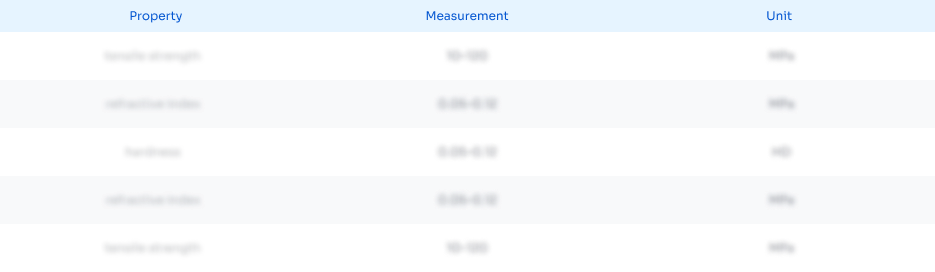
Abstract
Description
Claims
Application Information

- R&D
- Intellectual Property
- Life Sciences
- Materials
- Tech Scout
- Unparalleled Data Quality
- Higher Quality Content
- 60% Fewer Hallucinations
Browse by: Latest US Patents, China's latest patents, Technical Efficacy Thesaurus, Application Domain, Technology Topic, Popular Technical Reports.
© 2025 PatSnap. All rights reserved.Legal|Privacy policy|Modern Slavery Act Transparency Statement|Sitemap|About US| Contact US: help@patsnap.com