Catalyst drying kiln
A drying kiln and catalyst technology, which is applied in the direction of progressive dryers, drying machines, dryers, etc., can solve problems such as inability to automate production, uneven heating of products, and inability to accurately control temperature and humidity, and achieve compact and reasonable design and reduce The production cycle and the effect of reducing product deformation
- Summary
- Abstract
- Description
- Claims
- Application Information
AI Technical Summary
Problems solved by technology
Method used
Image
Examples
Embodiment Construction
[0019] The specific embodiments of the present invention will be further described below in conjunction with the accompanying drawings.
[0020] The following examples are only examples for clearly illustrating the present invention, rather than limiting the implementation of the present invention. For those of ordinary skill in the art, on the basis of the following descriptions, other different forms of changes or changes can also be made, and these obvious changes or changes that belong to the spirit of the present invention are still within the protection scope of the present invention middle.
[0021] according to Figure 1-4 As shown, a catalyst drying kiln, comprising: a kiln body 1, a product delivery system, a gas circulation control system, a temperature control system, and a humidity control system, is characterized in that: the kiln body 1 is a tunnel type, steel frame structure, and the The kiln head and the kiln tail of the kiln body are provided with automatic...
PUM
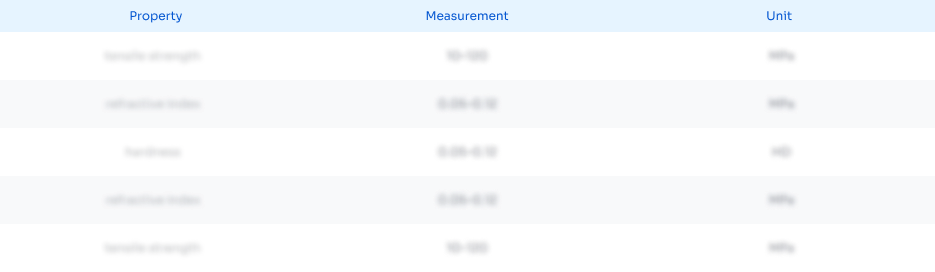
Abstract
Description
Claims
Application Information

- R&D
- Intellectual Property
- Life Sciences
- Materials
- Tech Scout
- Unparalleled Data Quality
- Higher Quality Content
- 60% Fewer Hallucinations
Browse by: Latest US Patents, China's latest patents, Technical Efficacy Thesaurus, Application Domain, Technology Topic, Popular Technical Reports.
© 2025 PatSnap. All rights reserved.Legal|Privacy policy|Modern Slavery Act Transparency Statement|Sitemap|About US| Contact US: help@patsnap.com