Ultra-large type combined H-section steel column and manufacturing method thereof
A production method and super-large technology, applied in the direction of columns, pier columns, pillars, etc., can solve the problems of difficult on-site processing, inconvenient transportation, and high requirements on the construction surface, so as to reduce the workload of assembly, facilitate cross-construction, and reduce the weight of the structure Effect
- Summary
- Abstract
- Description
- Claims
- Application Information
AI Technical Summary
Problems solved by technology
Method used
Image
Examples
Embodiment 1
[0034] Example 1: Such as figure 1 A super-large composite H-section steel column shown includes two I-beams 2 and a connecting web 1; the two I-beams 2 are respectively installed on both sides of the connecting web 1, and the section after installation is H-shaped ; Connect the upper end surface of the web 1 and the I-beams 2 on both sides to form a concave structure, and a stiffening plate 3 is arranged along the concave structure, and a reinforcing rod 4 is arranged on the stiffening plate 3; corbels are installed on the side of the I-beam 2 5 and stud 6; two I-beams 2 are not arranged in parallel, and the angle between them is 1.5. The ultra-large composite H-section steel column is made of Q345GJC-Z25 steel plate with a size of 4050x2350x70x80mm.
[0035] The above-mentioned ultra-large composite H-section steel column is made by the following method:
[0036] (1) Use a 2,000-ton hydraulic press to level the I-beam and connecting webs, use a CNC straight cutting machi...
PUM
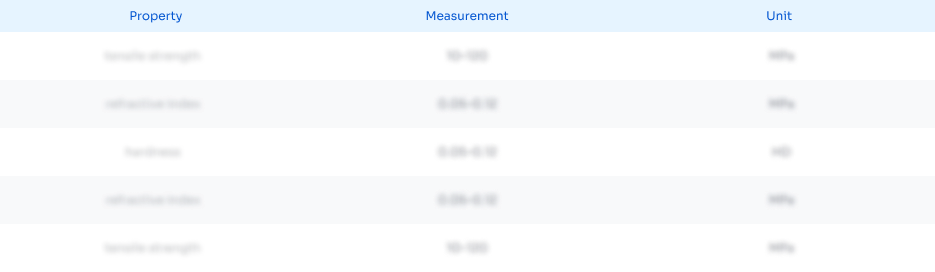
Abstract
Description
Claims
Application Information

- Generate Ideas
- Intellectual Property
- Life Sciences
- Materials
- Tech Scout
- Unparalleled Data Quality
- Higher Quality Content
- 60% Fewer Hallucinations
Browse by: Latest US Patents, China's latest patents, Technical Efficacy Thesaurus, Application Domain, Technology Topic, Popular Technical Reports.
© 2025 PatSnap. All rights reserved.Legal|Privacy policy|Modern Slavery Act Transparency Statement|Sitemap|About US| Contact US: help@patsnap.com