Steamed wood fiber aerated concrete block and preparation method thereof
A technology of air-entrained concrete and wood fiber, which is applied to ceramic products, climate sustainability, and other household appliances. It can solve problems such as reduced sound insulation effect, influence on material promotion, and cracking of plastering layers, so as to improve utilization rate, Reduced consumption and low production energy consumption
- Summary
- Abstract
- Description
- Claims
- Application Information
AI Technical Summary
Problems solved by technology
Method used
Examples
Embodiment 1
[0023] A method for preparing an autoclaved wood fiber aerated concrete block, comprising the following steps:
[0024] (1) Mix 5 parts of cement, 15 parts of quicklime, 5 parts of gypsum, 35 parts of fly ash, and 40 parts of wood fiber pulp in the mass ratio and mix them evenly, then add 60 parts of water and mix them for 2 hours to form a slurry;
[0025] (2) Add 0.7 parts of aluminum powder paste to the slurry and stir for 30s, the slurry will expand to form uniform and fine pores;
[0026] (3) The slurry in step (2) is statically stopped and precured for 1 hour, and the slurry is thickened and hardened into an aerated concrete body;
[0027] (4) Cut the concrete blank into block blanks, put them into an autoclave and cure them with high-pressure saturated steam for 10 hours to obtain finished products.
[0028] The mass percentage content of calcium oxide in the quicklime is 60-70%.
[0029] In the step (4), the pressure inside the autoclave is 1.5MPa, and the temperatur...
Embodiment 2
[0031] A method for preparing an autoclaved wood fiber aerated concrete block, comprising the following steps:
[0032] (1) Mix and stir 10 parts of cement, 17 parts of quicklime, 3 parts of gypsum, 40 parts of fly ash, and 30 parts of wood fiber pulp in mass proportion, and then add 65 parts of water to mix and stir for 3 hours to form a slurry;
[0033] (2) Add 0.75 parts of aluminum powder paste to the slurry and stir for 45s, the slurry will expand to form uniform and fine pores;
[0034] (3) The slurry in step (2) is statically stopped and pre-cured for 1.5 hours, and the slurry is thickened and hardened into an aerated concrete body;
[0035] (4) Cut the concrete blank into block blanks, send them into an autoclave and cure them with high-pressure saturated steam for 12 hours to obtain finished products.
[0036] The mass percentage content of calcium oxide in the quicklime is 60-70%.
[0037] In the step (4), the pressure inside the autoclave is 1.5MPa, and the temper...
Embodiment 3
[0039] A method for preparing an autoclaved wood fiber aerated concrete block, comprising the following steps:
[0040] (1) Mix 5 parts of cement, 20 parts of quicklime, 10 parts of gypsum, 30 parts of fly ash, and 35 parts of wood fiber pulp in the mass ratio and mix them evenly, then add 70 parts of water and mix them for 4 hours to form a slurry;
[0041] (2) Add 0.8 parts of aluminum powder paste to the slurry and stir for 60s, the slurry will expand to form uniform and fine pores;
[0042] (3) The slurry in step (2) is statically stopped and precured for 2 hours, and the slurry is thickened and hardened into an aerated concrete body;
[0043] (4) Cut the concrete blank into block blanks, send them into an autoclave and cure them with high-pressure saturated steam for 14 hours to obtain finished products.
[0044] The mass percentage content of calcium oxide in the quicklime is 60-70%.
[0045] In the step (4), the pressure inside the autoclave is 1.5MPa, and the tempera...
PUM
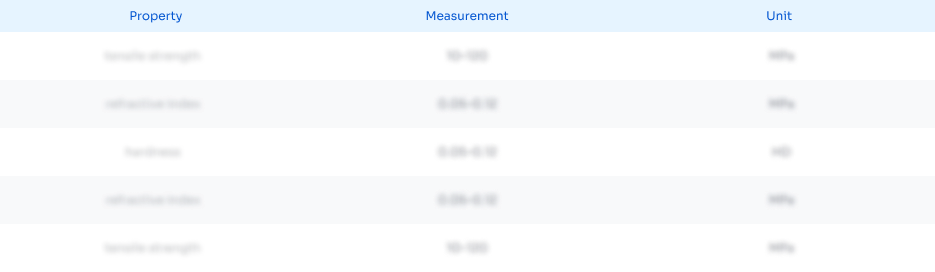
Abstract
Description
Claims
Application Information

- R&D Engineer
- R&D Manager
- IP Professional
- Industry Leading Data Capabilities
- Powerful AI technology
- Patent DNA Extraction
Browse by: Latest US Patents, China's latest patents, Technical Efficacy Thesaurus, Application Domain, Technology Topic, Popular Technical Reports.
© 2024 PatSnap. All rights reserved.Legal|Privacy policy|Modern Slavery Act Transparency Statement|Sitemap|About US| Contact US: help@patsnap.com