Magnetic suspension switch magnetic resistance flywheel motor and control method
A switched reluctance, flywheel motor technology, applied in the direction of a single motor speed/torque control, control system, control generator, etc., can solve the problem of limiting the critical maximum speed, poor radial force and torque decoupling effect, increasing the motor Axial length etc.
- Summary
- Abstract
- Description
- Claims
- Application Information
AI Technical Summary
Problems solved by technology
Method used
Image
Examples
Embodiment Construction
[0056] The present invention will be further described below in conjunction with the accompanying drawings.
[0057] figure 1 Shown is a schematic diagram of the working principle of the magnetic levitation switched reluctance flywheel motor system of the present invention. When the maglev switched reluctance flywheel motor is driven by the power electronic converter to drive the flywheel to accelerate the rotation, the flywheel stores electrical energy in the form of mechanical energy, and the flywheel system is in the charging mode. At this time, the motor operates as a motor; when there is no need to supply power to the outside, The speed of the flywheel motor is constant, the flywheel energy storage system is in the hold mode, and the motor is on standby at this time; when it is necessary to provide electric energy to the outside, the flywheel rotates at a high speed due to inertia and acts as the prime mover of the system to drag the motor in the system to generate electr...
PUM
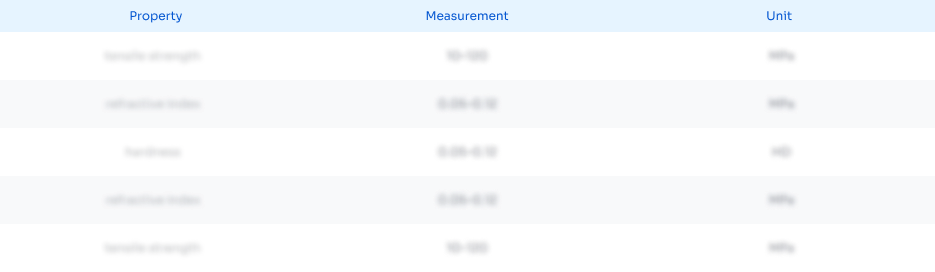
Abstract
Description
Claims
Application Information

- Generate Ideas
- Intellectual Property
- Life Sciences
- Materials
- Tech Scout
- Unparalleled Data Quality
- Higher Quality Content
- 60% Fewer Hallucinations
Browse by: Latest US Patents, China's latest patents, Technical Efficacy Thesaurus, Application Domain, Technology Topic, Popular Technical Reports.
© 2025 PatSnap. All rights reserved.Legal|Privacy policy|Modern Slavery Act Transparency Statement|Sitemap|About US| Contact US: help@patsnap.com