Mechanical fault diagnosis method adopting EASI algorithm based on independent component analysis
A technology of independent component analysis and diagnosis method, which is applied in the direction of calculation, measuring device, and measurement of ultrasonic/sonic wave/infrasonic wave, etc., which can solve the problems that cannot be extracted, difficult to extract characteristic signals, single and independent mechanical fault signals, etc., and achieve the solution of characteristic signal extraction problem effect
- Summary
- Abstract
- Description
- Claims
- Application Information
AI Technical Summary
Problems solved by technology
Method used
Image
Examples
Embodiment Construction
[0033] Below in conjunction with the accompanying drawings, the method and the technical solution of the present invention are further elaborated, reference signs: 1 spring; 2 brake; 3 wheel; 4 acceleration sensor; 5 gear 1; 6 gear 2; 7 gear 3; 8 gear 4; 9 reducer Ⅰ; 10 reducer Ⅱ; 11 reducer Ⅲ; 12 charge amplifier; 13 computer; 14 AC motor; 15 torque sensor; 16 frequency converter; 17 acceleration sensor 1; 18 acceleration sensor 2; 19 acceleration sensor 3 ; 20 acceleration sensor 4; 21 acceleration sensor 5; 22 acceleration sensor 6.
[0034] The invention relates to a bearing mechanical fault diagnosis method based on independent component analysis.
[0035] (1) Acceleration sensors are used to collect acceleration signals at different points on the gearbox. It is required that the number of sensors collecting signals is not less than the total number of bearings and gears, and then use an amplifier to amplify each signal, and then use an analog-to-digital converter to conv...
PUM
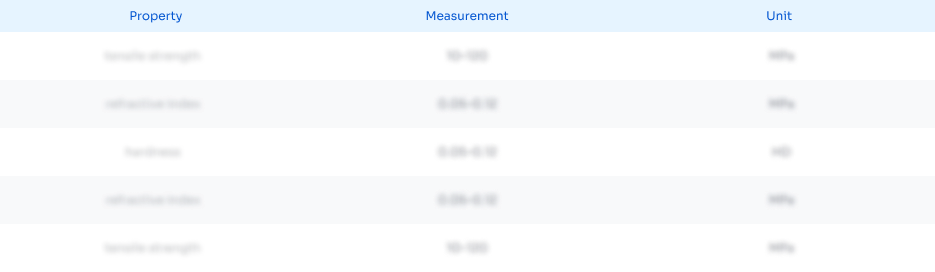
Abstract
Description
Claims
Application Information

- Generate Ideas
- Intellectual Property
- Life Sciences
- Materials
- Tech Scout
- Unparalleled Data Quality
- Higher Quality Content
- 60% Fewer Hallucinations
Browse by: Latest US Patents, China's latest patents, Technical Efficacy Thesaurus, Application Domain, Technology Topic, Popular Technical Reports.
© 2025 PatSnap. All rights reserved.Legal|Privacy policy|Modern Slavery Act Transparency Statement|Sitemap|About US| Contact US: help@patsnap.com