Pure-cotton fabric biological enzyme scouring and bleaching one-bath process
A technology of knitted fabrics and biological enzymes, which is applied in the pretreatment process of pure cotton knitted fabrics, can solve the problems of large wastewater discharge, low efficiency, and long process, and achieve the effects of shortening the process flow, broad market prospects, and easy biodegradation
- Summary
- Abstract
- Description
- Claims
- Application Information
AI Technical Summary
Problems solved by technology
Method used
Examples
Embodiment 1
[0026] A one-bath biological enzymatic scouring and bleaching process for pure cotton knitted fabrics, comprising the following steps: (1) Weighing 4.0 g of scouring enzyme, cutinase, cellulase and pectinase compound enzyme, 10 mL of 30% hydrogen peroxide, 10g of urea is used to make an enzyme oxygen bleaching solution with a pH value of 10, and the pure cotton knitted fabric is weighed, and the bath ratio of the pure cotton knitted fabric to the enzyme oxygen bleaching solution is 1:8; (2) the pure cotton Put the knitted gray fabric into a heater at 89°C for pretreatment and heat for 9 minutes; (3) Put the pretreated pure cotton knitted fabric into an enzyme oxygen cooking and bleaching solution, and boil it in a heater at a temperature of 89°C Bleaching for 70 minutes; (4) Put the boiled and bleached pure cotton knitted fabric in an organic acid at a temperature of 48°C for neutralization and washing for 82 minutes; (5) Put the neutralized and washed pure cotton knitted fabri...
Embodiment 2
[0028] A one-bath biological enzymatic scouring and bleaching process for pure cotton knitted fabrics, comprising the following steps: (1) Weighing 4.5g of scouring enzyme, cutinase, cellulase and pectinase compound enzyme, 15mL of 30% hydrogen peroxide, 15g of urea is used to make an enzyme oxygen bleaching solution with a pH value of 10.2, and the pure cotton knitted fabric is weighed, and the bath ratio of the pure cotton knitted fabric to the enzyme oxygen bleaching solution is 1:8; (2) Pure cotton Put the knitted gray fabric into a heater at 90°C for pretreatment and heat for 10 minutes; (3) Put the pretreated pure cotton knitted fabric into an enzyme oxygen cooking and bleaching solution, and boil it in a heater at a temperature of 90°C Bleaching for 75 minutes; (4) Put the boiled and bleached pure cotton knitted fabric in an organic acid at a temperature of 50°C for neutralization and washing for 10 minutes; (5) Put the neutralized and washed pure cotton knitted fabric f...
Embodiment 3
[0030] A one-bath biological enzymatic scouring and bleaching process for pure cotton knitted fabrics, comprising the following steps: (1) Weighing 5.0 g of scouring enzyme, cutinase, cellulase and pectinase compound enzyme, 20 mL of 30% hydrogen peroxide, 20g of urea is used to make an enzyme oxygen bleaching solution with a pH value of 10.5, and the pure cotton knitted fabric is weighed, and the bath ratio of the pure cotton knitted fabric to the enzyme oxygen bleaching solution is 1:8; (2) Pure cotton Put the knitted gray fabric into a heater at 91°C for pretreatment and heat for 11 minutes; (3) Put the pretreated pure cotton knitted fabric into an enzyme oxygen cooking and bleaching solution, and boil it in a heater at a temperature of 91°C Bleaching for 80 minutes; (4) Put the boiled and bleached pure cotton knitted fabric in an organic acid at a temperature of 52°C for neutralization and washing for 12 minutes; (5) Put the neutralized and washed pure cotton knitted fabric...
PUM
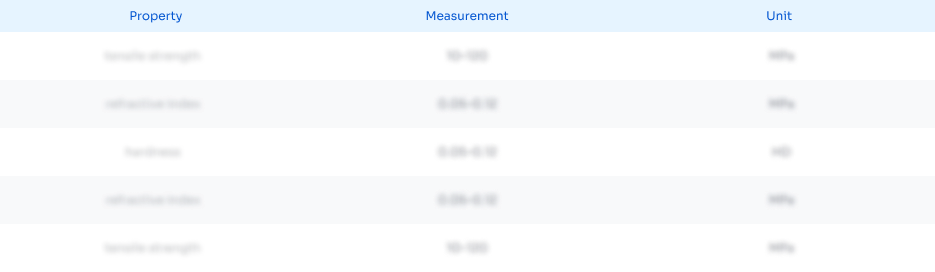
Abstract
Description
Claims
Application Information

- R&D
- Intellectual Property
- Life Sciences
- Materials
- Tech Scout
- Unparalleled Data Quality
- Higher Quality Content
- 60% Fewer Hallucinations
Browse by: Latest US Patents, China's latest patents, Technical Efficacy Thesaurus, Application Domain, Technology Topic, Popular Technical Reports.
© 2025 PatSnap. All rights reserved.Legal|Privacy policy|Modern Slavery Act Transparency Statement|Sitemap|About US| Contact US: help@patsnap.com