Modularized joint for hollow series-connection mechanical arm
A technology of modular joints and mechanical arms, applied in the field of robotics, can solve the problems of unfavorable construction of a mechanical arm with a range of motion, inability to achieve instantaneous braking, and a single connection method, achieving high transmission accuracy and carrying capacity, compact structure, and simplified internal effect of structure
- Summary
- Abstract
- Description
- Claims
- Application Information
AI Technical Summary
Problems solved by technology
Method used
Image
Examples
Embodiment approach
[0013] As shown in the accompanying drawings, the modular joint for the hollow series mechanical arm of the present invention includes a housing 14, a rear cover 15 is installed on the housing 14 and an opening is provided on one side of the housing 14. A bracket 8 is installed in the housing 14, a servo motor 1 and a tensioning mechanism are installed on the top surface of the bracket 8, and the speed reducer 5 is fixed on the housing 14 below the bracket 8. The mechanism includes a bearing seat 13, in which the joint tension shaft 10 is installed through upper and lower bearings 11, 12, and the described bearing seat 13 is supported and fixed on the belt pulley tension swing rod 9, and the belt pulley The wheel tension swing lever 9 is rotatably connected to the bracket 8 through the installation shaft, and the power-off brake 2 is installed on the bearing seat, and one end of the joint tension shaft 10 is fixedly connected with the rotor of the power-off brake through the ro...
PUM
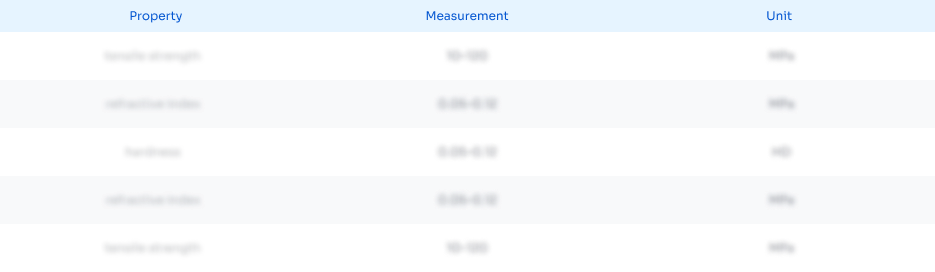
Abstract
Description
Claims
Application Information

- Generate Ideas
- Intellectual Property
- Life Sciences
- Materials
- Tech Scout
- Unparalleled Data Quality
- Higher Quality Content
- 60% Fewer Hallucinations
Browse by: Latest US Patents, China's latest patents, Technical Efficacy Thesaurus, Application Domain, Technology Topic, Popular Technical Reports.
© 2025 PatSnap. All rights reserved.Legal|Privacy policy|Modern Slavery Act Transparency Statement|Sitemap|About US| Contact US: help@patsnap.com