Visual quantitative calibration and analysis method for cutter abrasion of shield tunneling machine
A shield machine tool and analysis method technology, which is applied in the field of shield machine tool wear detection, can solve problems such as incomplete detection of tool wear sensing devices, inaccurate analysis methods of tunneling parameters, and poor effect of odor additives, etc., achieving important economic benefits. and social benefits, reducing engineering safety risks, and the effects of major engineering significance
- Summary
- Abstract
- Description
- Claims
- Application Information
AI Technical Summary
Problems solved by technology
Method used
Image
Examples
Embodiment Construction
[0025] The present invention will be further described below in conjunction with the accompanying drawings and specific embodiments.
[0026] like figure 1 As shown, a visual quantitative calibration and analysis method for shield machine tool wear, specifically includes three parts: the construction of a precise 3D model of the shield machine, the attitude calculation of the detection image data, and the restoration of the spatial scene structure. Among them: the construction of the precise 3D model includes two steps of constructing the basic framework of the shield machine model and the refinement of the 3D model, the attitude calculation of the detection image data includes three steps of camera calibration, image acquisition and attitude calculation, and the restoration of the space scene structure It includes three steps of image processing, orientation operation and quantitative detection of tool wear.
[0027] The specific operation steps are as follows:
[0028] 1. ...
PUM
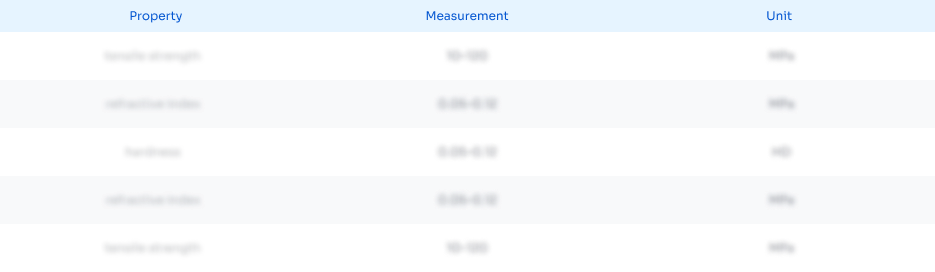
Abstract
Description
Claims
Application Information

- R&D
- Intellectual Property
- Life Sciences
- Materials
- Tech Scout
- Unparalleled Data Quality
- Higher Quality Content
- 60% Fewer Hallucinations
Browse by: Latest US Patents, China's latest patents, Technical Efficacy Thesaurus, Application Domain, Technology Topic, Popular Technical Reports.
© 2025 PatSnap. All rights reserved.Legal|Privacy policy|Modern Slavery Act Transparency Statement|Sitemap|About US| Contact US: help@patsnap.com