Packaging method of flat rolled toilet paper
A packaging method and technology for toilet paper, applied in the field of toilet paper packaging, can solve problems such as affecting product packaging, warping at both ends of the product, and small contact area, and achieve the effect of saving space
- Summary
- Abstract
- Description
- Claims
- Application Information
AI Technical Summary
Problems solved by technology
Method used
Image
Examples
Embodiment 1
[0036] As a preferred embodiment of the present invention, with reference to the attached figure 1 , the steps of the present invention are as follows:
[0037]The first step, crushing: the material is conveyed by the conveying device 1 to the first crushing mechanism 2, the material is crushed in the first crushing mechanism 2, and the material crushed by the first crushing mechanism 2 is conveyed to the steering device by the conveying device 1 At 6, the material is turned over by the turning device 6 at both ends, and the turned material is transported by the conveying device 1 to the secondary flattening mechanism 3 for secondary flattening;
[0038] The second step, stacking: the material after secondary flattening is transported to the first pushing platform 10 and the second pushing platform 11 on both sides of the main conveying mechanism 9 through two side conveying mechanisms 8. The material on the pushing platform 10 is pushed onto the main conveying mechanism 9, a...
Embodiment 2
[0043] As another preferred embodiment of the present invention, refer to the attached figure 1 and 2 , the steps of the present invention are as follows:
[0044] The first step, crushing: the material is conveyed by the conveying device 1 to the first crushing mechanism 2, the material is crushed in the first crushing mechanism 2, and the material crushed by the first crushing mechanism 2 is conveyed to the steering device by the conveying device 1 At 6, the material is turned over by the turning device 6 at both ends, and the turned material is transported by the conveying device 1 to the secondary flattening mechanism 3 for secondary flattening;
[0045] The second step, stacking: the material after secondary flattening is transported to the first pushing platform 10 and the second pushing platform 11 on both sides of the main conveying mechanism 9 through two side conveying mechanisms 8. The material on the pushing platform 10 is pushed onto the main conveying mechanism...
Embodiment 3
[0058] As another preferred embodiment of the present invention, with reference to the attached figure 1 , 3 And 4, the steps of the present invention are as follows:
[0059] The first step, crushing: the material is conveyed by the conveying device 1 to the first crushing mechanism 2, the material is crushed in the first crushing mechanism 2, and the material crushed by the first crushing mechanism 2 is conveyed to the steering device by the conveying device 1 At 6, the material is turned over by the turning device 6 at both ends, and the turned material is transported by the conveying device 1 to the secondary flattening mechanism 3 for secondary flattening;
[0060] The second step, stacking: the material after secondary flattening is transported to the first pushing platform 10 and the second pushing platform 11 on both sides of the main conveying mechanism 9 through two side conveying mechanisms 8. The material on the pushing platform 10 is pushed onto the main conveyi...
PUM
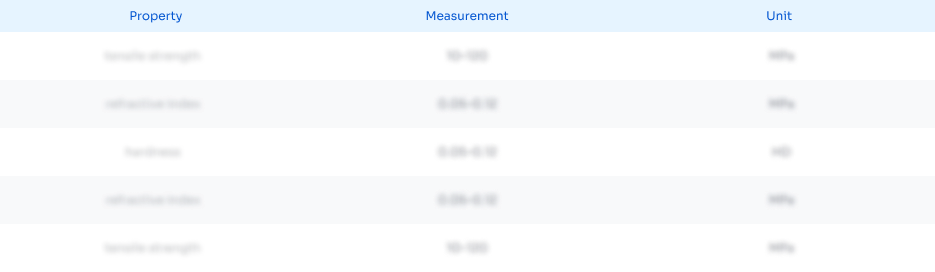
Abstract
Description
Claims
Application Information

- R&D Engineer
- R&D Manager
- IP Professional
- Industry Leading Data Capabilities
- Powerful AI technology
- Patent DNA Extraction
Browse by: Latest US Patents, China's latest patents, Technical Efficacy Thesaurus, Application Domain, Technology Topic, Popular Technical Reports.
© 2024 PatSnap. All rights reserved.Legal|Privacy policy|Modern Slavery Act Transparency Statement|Sitemap|About US| Contact US: help@patsnap.com