Ultrathin strip rolling mill adopting support roller transmission and rolling method of ultrathin strip rolling mill
A technology of support rolls and ultra-thin strips, applied in metal rolling, metal rolling, metal rolling stands, etc., can solve problems such as limited rolling capacity of rolling mills, pinion modulus, torsional vibration, etc., and achieve rolling Increased thickness range, small variable step size, and reduced torsional vibration
- Summary
- Abstract
- Description
- Claims
- Application Information
AI Technical Summary
Problems solved by technology
Method used
Image
Examples
Embodiment Construction
[0035] The present invention will be further described in detail below in conjunction with the accompanying drawings and specific embodiments.
[0036] Such as figure 1 , 2 As shown, an ultra-thin strip rolling mill that adopts back-up roll transmission includes a main drive motor 1, a work roll, a back-up roll, a pressing device 7, an archway 8, a first tension motor 19 and a second tension motor 22, and the working The rolls include an upper work roll 2 and a lower work roll 3, and the support rolls include an upper support roll 4 and a lower support roll 5. Both the upper work roll 2 and the lower work roll 3 are slidingly connected with the archway 8 through the work roll bearing housing 17, and the upper The support roll 4 is fixed in the window of the archway 8 through the support roll bearing seat 18, and the lower support roll 5 is fixed at the bottom of the archway 8 through the support roll bearing seat 18, between the work roll bearing seat 17 of the upper work rol...
PUM
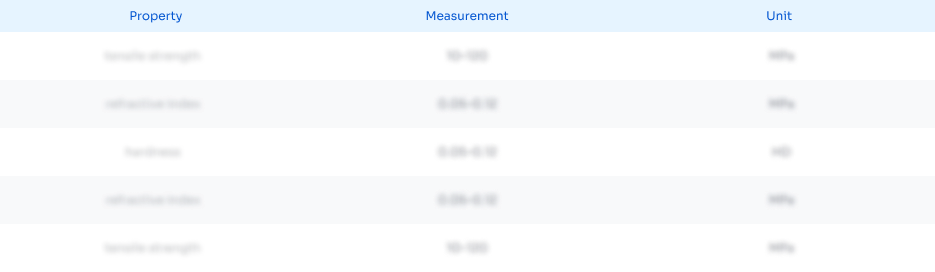
Abstract
Description
Claims
Application Information

- Generate Ideas
- Intellectual Property
- Life Sciences
- Materials
- Tech Scout
- Unparalleled Data Quality
- Higher Quality Content
- 60% Fewer Hallucinations
Browse by: Latest US Patents, China's latest patents, Technical Efficacy Thesaurus, Application Domain, Technology Topic, Popular Technical Reports.
© 2025 PatSnap. All rights reserved.Legal|Privacy policy|Modern Slavery Act Transparency Statement|Sitemap|About US| Contact US: help@patsnap.com