Hybrid electromagnetic magnetic bearing switch reluctance motor
A technology of switched reluctance motor and reluctance motor, which is applied in the direction of electrical components, electromechanical devices, magnetic attraction or thrust holding devices, etc., and can solve the problems of large demand for suspension winding enameled wire, low power density, and low utilization of windings , to achieve the effects of good real-time control of current, strong high-speed adaptability, and large radial suspension force
- Summary
- Abstract
- Description
- Claims
- Application Information
AI Technical Summary
Problems solved by technology
Method used
Image
Examples
Embodiment Construction
[0025] The technical scheme of the present invention is described in detail below in conjunction with accompanying drawing:
[0026] Such as figure 1 As shown, a structural schematic diagram of a hybrid electric excitation magnetic bearing switched reluctance motor of the present invention, wherein, 1 is the stator core of the reluctance motor, 2 is the rotor core of the reluctance motor, 3 is the stator core of the magnetic bearing, and 4 is the magnetic bearing Rotor core, 5 is the torque winding, 6 is the suspension force winding, 7 is the rotating shaft.
[0027] The motor stator is composed of a reluctance motor stator and a magnetic bearing stator, both of which have a salient pole structure, and the number of teeth is 12; the reluctance motor stator and the magnetic bearing stator are in a tooth-to-tooth alignment state, and both axial separated by a distance greater than the end length of the levitation force winding;
[0028] The motor rotor is composed of a relucta...
PUM
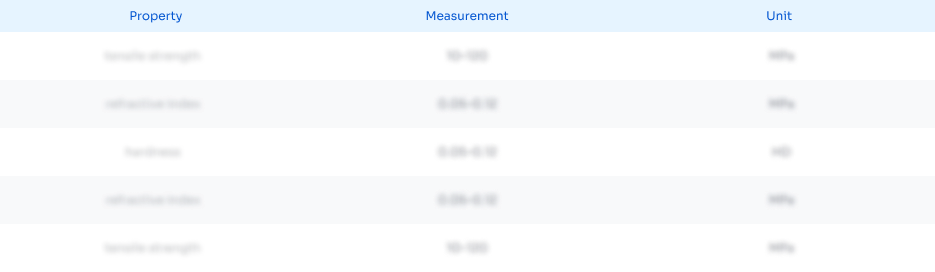
Abstract
Description
Claims
Application Information

- R&D
- Intellectual Property
- Life Sciences
- Materials
- Tech Scout
- Unparalleled Data Quality
- Higher Quality Content
- 60% Fewer Hallucinations
Browse by: Latest US Patents, China's latest patents, Technical Efficacy Thesaurus, Application Domain, Technology Topic, Popular Technical Reports.
© 2025 PatSnap. All rights reserved.Legal|Privacy policy|Modern Slavery Act Transparency Statement|Sitemap|About US| Contact US: help@patsnap.com