Vibration-sensing structures with temperature compensation based on surface acoustic waves
A technology of surface acoustic wave and temperature compensation, applied in the direction of measuring ultrasonic/sonic/infrasonic waves, measuring devices, instruments, etc., can solve the problems of not being able to monitor vibration and not having temperature compensation function, and achieve simple structure and low production cost , the effect of high measurement accuracy
- Summary
- Abstract
- Description
- Claims
- Application Information
AI Technical Summary
Problems solved by technology
Method used
Image
Examples
Embodiment Construction
[0023] The present invention will be further described below in conjunction with the accompanying drawings and given embodiments, but is not limited thereto.
[0024] Such as figure 1 , 2 , 3, a sensing vibration sensing structure with temperature compensation based on surface acoustic waves, including a housing 1 and a housing cover 2, the housing 1 and the housing cover 2 are hermetically connected, and it:
[0025] a. It also includes a base 8, a piezoelectric substrate 3 and three surface acoustic wave resonators 4, and the base 8 is fixed on the bottom of the housing 1;
[0026] b. One end of the piezoelectric substrate 3 is a fixed end, and the other end is a cantilevered end. The fixed end of the piezoelectric substrate 3 is fixed on the base 8 and is higher than the bottom surface of the housing 1,
[0027] The three surface acoustic wave resonators 4 are all arranged on the upper surface of the piezoelectric substrate 3;
[0028] c. The three surface acoustic wave ...
PUM
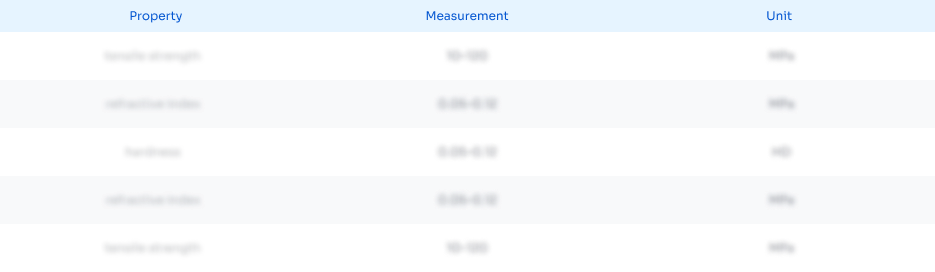
Abstract
Description
Claims
Application Information

- R&D
- Intellectual Property
- Life Sciences
- Materials
- Tech Scout
- Unparalleled Data Quality
- Higher Quality Content
- 60% Fewer Hallucinations
Browse by: Latest US Patents, China's latest patents, Technical Efficacy Thesaurus, Application Domain, Technology Topic, Popular Technical Reports.
© 2025 PatSnap. All rights reserved.Legal|Privacy policy|Modern Slavery Act Transparency Statement|Sitemap|About US| Contact US: help@patsnap.com