Photoactive polylactic acid acrylate degradation material
A technology of lactic acid acrylate and degradable materials, which can be used in applications, coatings, inks, etc., can solve the problems of limiting the use and promotion of polylactic acid, complicated processes, and high cost of polylactic acid, achieving excellent comprehensive performance, expanding the scope of application, and degrading The effect of speed reduction
- Summary
- Abstract
- Description
- Claims
- Application Information
AI Technical Summary
Problems solved by technology
Method used
Image
Examples
Embodiment 1
[0031] Add 100 parts of lactic acid (purity > 95%) into the reaction kettle, at 120°C, vacuumize the reaction system to control the pressure of the reaction system at 50-30KPa, react for 2 hours, and remove the moisture generated by the system to obtain the polylactic acid prepolymer; Add 1 part of pentaerythritol, 0.5 part of SnCl to the system 2 +TSA (mass ratio SnCl 2 : TSA= 1:1) composite catalyst, the temperature was raised to 180°C, the pressure inside the reactor was kept at 30-10 KPa, and the reaction was carried out for 8 hours to obtain hydroxyl-terminated polylactic acid. Add 100 parts of hydroxyl-terminated polylactic acid and 50 parts of toluene into the reactor, raise the temperature to 90°C, and gradually add 10 parts of acrylic acid, 0.5 parts of p-toluenesulfonic acid and 0.15 parts of hydroquinone polymerization inhibitor within 0.5 hours. Then the temperature was raised to 130° C., the pressure in the reactor was kept at 30-10 KPa, and the reaction was carr...
Embodiment 2
[0033] Add 100 parts of lactic acid (purity > 95%) into the reaction kettle, at 120°C, vacuumize the reaction system to control the pressure of the reaction system at 50-30KPa, react for 4 hours, remove the moisture generated by the system to obtain a polylactic acid prepolymer; add 10 Parts of diethylene glycol and 0.5 parts of SnCl 2 +TSA (mass ratio SnCl 2: TSA= 1:1) composite catalyst, heat up to 140°C, keep the pressure in the reactor at 30-5 KPa, react for 4 hours to obtain hydroxyl-terminated polylactic acid; then add 100 parts of hydroxyl-terminated polylactic acid and 30 parts of toluene into the reactor , the temperature was raised to 90°C, and 30 parts of acryloyl chloride, 1 part of p-toluenesulfonic acid and 0.1 part of hydroquinone inhibitor were gradually added in 0.5 hours. Then heat up to 140°C, keep the pressure in the reactor at 30-5 KPa, and react for 3 hours to obtain active polylactic acid acrylate with terminal double bonds; mix polylactic acid acrylate...
Embodiment 3
[0035] Add 100 parts of lactic acid (purity > 95%) into the reactor, at 120°C, vacuum control the pressure of the reaction system at 70-50KPa, react for 6 hours, remove the moisture generated by the system to obtain a polylactic acid prepolymer; add 35 Part ethylene glycol, 0.5 part SnCl 2 +TSA (mass ratio SnCl 2 : TSA= 1:1) composite catalyst, heat up to 200°C, keep the pressure in the reactor at 50-30 KPa, react for 12 hours, refine the reactant to obtain hydroxyl-terminated polylactic acid; then mix 100 parts of hydroxyl-terminated polylactic acid, 90 parts Add toluene to the reaction kettle, raise the temperature to 90°C, gradually add 1 part of methacrylic anhydride, 5 parts of p-toluenesulfonic acid and 0.5 parts of hydroquinone polymerization inhibitor within 0.5 hours. Then the temperature was raised to 110° C., the pressure in the reactor was kept at 50-30 KPa, and the reaction was carried out for 8 hours to obtain terminal double bond active polylactic acid acrylate...
PUM
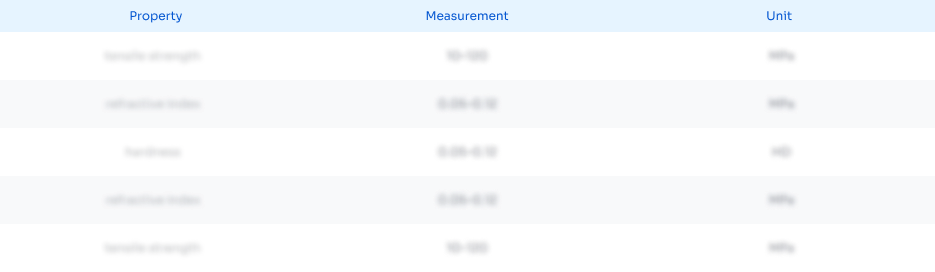
Abstract
Description
Claims
Application Information

- R&D
- Intellectual Property
- Life Sciences
- Materials
- Tech Scout
- Unparalleled Data Quality
- Higher Quality Content
- 60% Fewer Hallucinations
Browse by: Latest US Patents, China's latest patents, Technical Efficacy Thesaurus, Application Domain, Technology Topic, Popular Technical Reports.
© 2025 PatSnap. All rights reserved.Legal|Privacy policy|Modern Slavery Act Transparency Statement|Sitemap|About US| Contact US: help@patsnap.com