Mould pressing floor board and manufacturing method and mould thereof
A manufacturing method and molding technology, which is applied in the manufacture of molded floors and the field of molds for manufacturing molded floors, can solve the problems of low electricity and equipment investment costs, easy wear of tools, and affect installation, etc., to achieve small loss of effective area and accuracy of product shape High, the effect of saving manufacturing costs
- Summary
- Abstract
- Description
- Claims
- Application Information
AI Technical Summary
Problems solved by technology
Method used
Image
Examples
Embodiment 1
[0045] Such as figure 1 , figure 2 , image 3 As shown, a molded floor includes a surface composite layer 1 and a base material layer 9 stacked up and down, and a tongue and a tongue and groove are respectively provided on the opposite side walls, and one side of the base material layer 9 is provided with There is an upper extension 10 extending outwardly from the surface composite layer 1 along the upper surface of the base material layer 9, and on the opposite side, a Extended lower extension 11, the tongue is composed of a front tongue section 4 and a rear tongue section 21, wherein the front tongue section 4 is located on the upper extension 10 outside the surface composite layer 1 and the rear tongue section 21 On the upper extension part 10 below the surface composite layer 1, the tongue and groove is composed of a tongue and groove front section matched with the tongue front section 4 and a tongue and groove rear section matched with the tongue rear section 21, and t...
Embodiment 2
[0059] Such as Figure 4 As shown, the difference between this embodiment and Embodiment 1 is that the molded floor further includes an adhesive layer 22 disposed between the surface composite layer 1 and the base material layer 9 . Correspondingly, the manufacturing method of the molded floor further includes the step of setting an adhesive layer between the surface composite layer 1 and the base material layer 9 in step c. Other technical features are the same as those in Embodiment 1, and will not be repeated here.
[0060] In this embodiment, the surface composite layer 1 and the base material layer 9 are stacked up and down after molding respectively, and the lower surface of the surface composite layer 1 and / or the upper surface of the base material layer 9 are coated with an adhesive and cured to form a bond. Agent layer 22, so that it is firmly connected as a molded floor through the adhesive layer 22 between the surface composite layer 1 and the base material layer 9...
Embodiment 3
[0062] Such as Figure 5 , Figure 6 , Figure 7 As shown, the difference between this embodiment and Embodiment 1 or 2 is that the base material layer 9 is composed of the base material upper layer 2 and the base material lower layer 3, and the upper extension 10 is located on the side of the base material upper layer 2 Above, the lower extension 11 is located on the opposite side of the base material lower layer 3; the corresponding molded floor manufacturing method, in step b: molding the base material upper layer 2 with the upper extension 10 and the base material upper layer 2 with the lower extension 11, the base material lower layer 3, the base material upper layer 2 and the base material lower layer 3 are stacked up and down and bonded or molded to form the base material layer. Described composite negative plate 15 comprises the first negative plate 17 and the first male plate 16 that have the molded surface 20 that is used in relative cooperation, and described conc...
PUM
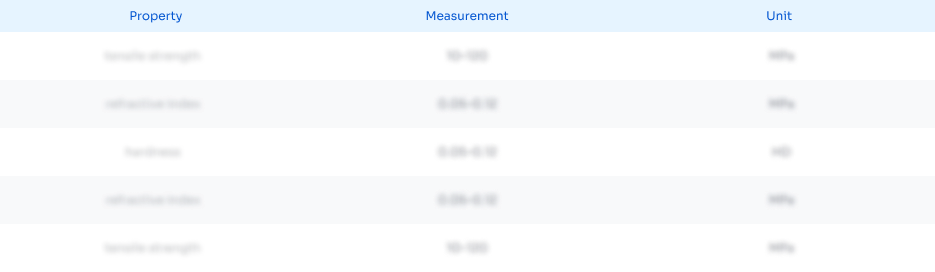
Abstract
Description
Claims
Application Information

- R&D Engineer
- R&D Manager
- IP Professional
- Industry Leading Data Capabilities
- Powerful AI technology
- Patent DNA Extraction
Browse by: Latest US Patents, China's latest patents, Technical Efficacy Thesaurus, Application Domain, Technology Topic, Popular Technical Reports.
© 2024 PatSnap. All rights reserved.Legal|Privacy policy|Modern Slavery Act Transparency Statement|Sitemap|About US| Contact US: help@patsnap.com