Preparation method of catalyst for preparing 2-methyltetrahydrofuran from 2-methylfuran through gas phase hydrogenation
A technology of methyl tetrahydrofuran catalyst and methyl furan, applied in the direction of metal/metal oxide/metal hydroxide catalyst, chemical instrument and method, physical/chemical process catalyst, etc., can solve the problem of increasing production cost, low reaction pressure, Environmental pollution and other problems, to achieve good stability, high selectivity, good repeatability
- Summary
- Abstract
- Description
- Claims
- Application Information
AI Technical Summary
Benefits of technology
Problems solved by technology
Method used
Examples
Embodiment 1
[0020] Example 1 Dissolve 34.02 grams of nickel nitrate 6 water in 234 ml of deionized water, add the solution dropwise to 105 grams of 25% silica sol at room temperature, wait for 2 hours after gelation, and then stir and evaporate the solvent at 80°C , dried at 100°C for 12 hours to obtain a xerogel, ground and extruded, and then calcined at 600°C for 4 hours in a muffle furnace to obtain a catalyst.
Embodiment 2
[0021] Example 2 Dissolve 40.7 grams of nickel nitrate 6 water in 280 ml of deionized water, add the solution dropwise to 98 grams of 25% silica sol at room temperature, age for 2 hours after gelation, then stir and evaporate the solvent at 80°C , dried at 100°C for 12 hours to obtain a xerogel, ground and extruded, and then calcined at 600°C for 4 hours in a muffle furnace to obtain a catalyst.
Embodiment 3
[0022] Example 3 Dissolve 34.02 grams of nickel nitrate 6 water and 2.95 grams of calcium nitrate 4 water in 259 ml of deionized water, add the solution dropwise to 102.2 grams of 25% silica sol at room temperature, and age for 2 hours after gelation, and then in The solvent was evaporated by stirring at 80°C, dried at 100°C for 12 hours to obtain a xerogel, ground and extruded, and then calcined in a muffle furnace at 600°C for 4 hours to obtain a catalyst.
PUM
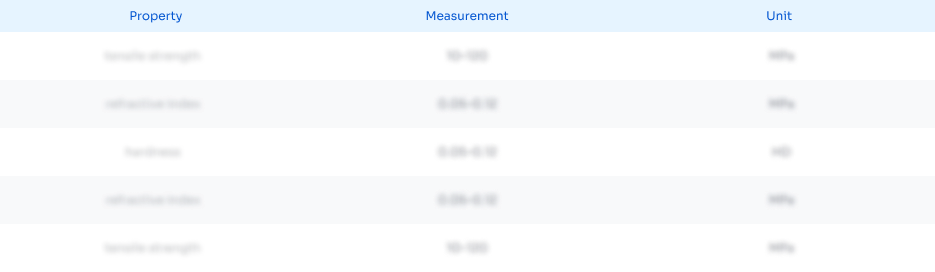
Abstract
Description
Claims
Application Information

- R&D Engineer
- R&D Manager
- IP Professional
- Industry Leading Data Capabilities
- Powerful AI technology
- Patent DNA Extraction
Browse by: Latest US Patents, China's latest patents, Technical Efficacy Thesaurus, Application Domain, Technology Topic, Popular Technical Reports.
© 2024 PatSnap. All rights reserved.Legal|Privacy policy|Modern Slavery Act Transparency Statement|Sitemap|About US| Contact US: help@patsnap.com