Treatment method for water containing vanadium, chromium and iron and smelting process for high chromium vanadium titanium magnetite concentrate
A technology for vanadium-titanium magnetite concentrate and vanadium-chromium molten iron, which is applied in the direction of improving process efficiency and can solve the problems of high silicon content and low carbon content.
- Summary
- Abstract
- Description
- Claims
- Application Information
AI Technical Summary
Problems solved by technology
Method used
Examples
example 1
[0027] The ladle contains 17.5 tons of vanadium-chromium-containing molten iron, the initial composition is [C] content of 2.51%, [Si] content of 0.58%, [Ti] content of 0.11%, the initial temperature is 1380 ° C, the calculated liquidus temperature of the molten iron T theory is 1313°C. It is designed to reduce the [Si] content by 0.18%, and the added amount of oxide scale desiliconization agent is calculated to be 0.237t. The molten iron does not need to be heated, and the desiliconizing agent is added in 3 times at about 0.08t each time within 12 minutes. After the time is reached, the amount of oxygen blowing is 30Nm 3 / ton of iron control, the calculated oxygen blowing time is 13 minutes, and 595kg of cold solidified pellets are added in three times 2 minutes before the end of oxygen blowing as a coolant for vanadium and chromium extraction. The actual temperature of molten iron during oxygen blowing is 1346 ° C ~ 1390 ° C. Finally, the V in the vanadium chromium slag 2...
example 2
[0029] The ladle contains 23.6 tons of vanadium-chromium-containing molten iron, the initial composition is [C] content of 1.37%, [Si] content of 0.39%, [Ti] content of 0.07%, the initial temperature is 1450 ° C, the calculated liquidus temperature of the molten iron T 理 It is 1409°C. It is designed to reduce the [Si] content by 0.09%, and the calculated amount of iron scale desiliconization agent is 0.18t. LF furnace heats molten iron to 1491°C, adds desiliconization agent twice in 8 minutes at about 0.09t each time, after the time is reached and slag is removed, the amount of oxygen blowing is 25Nm 3 / ton of iron control, the calculated oxygen blowing time is 22 minutes, and 650kg of cold solidified pellets are added in 5 times 2 minutes before the end of oxygen blowing as a coolant for vanadium and chromium extraction. The actual temperature of molten iron during oxygen blowing is 1442 ℃ ~ 1485 ℃. V in the final vanadium chromium slag 2 o 5 The content is 10.9%, Cr 2 ...
PUM
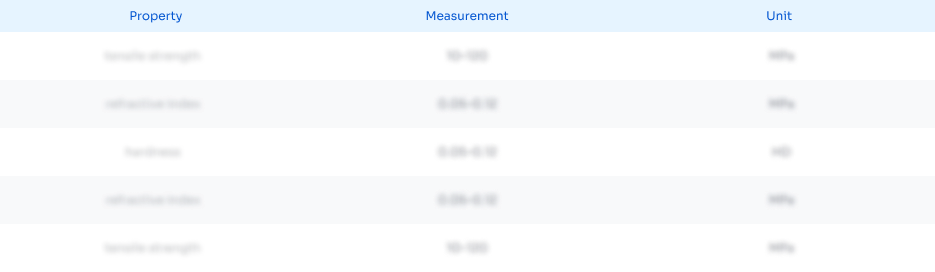
Abstract
Description
Claims
Application Information

- R&D Engineer
- R&D Manager
- IP Professional
- Industry Leading Data Capabilities
- Powerful AI technology
- Patent DNA Extraction
Browse by: Latest US Patents, China's latest patents, Technical Efficacy Thesaurus, Application Domain, Technology Topic, Popular Technical Reports.
© 2024 PatSnap. All rights reserved.Legal|Privacy policy|Modern Slavery Act Transparency Statement|Sitemap|About US| Contact US: help@patsnap.com