Multi-lead-screw parallel drive device
A driving device and lead screw technology, which is applied in the direction of transmission, belt/chain/gear, mechanical equipment, etc., can solve the problems of decreasing the accuracy of the mechanical device, increasing the local stress and working strength of the parts, and reducing the mechanical performance of the device. Low manufacturing accuracy and installation accuracy, lower manufacturing costs, and good dynamic performance
- Summary
- Abstract
- Description
- Claims
- Application Information
AI Technical Summary
Problems solved by technology
Method used
Image
Examples
Embodiment 1
[0014] like figure 1 As shown, the device includes four gears 1, first-stage slider guide rail 2, lead screw 3, first-stage connecting rod 4, first-stage slider 5, lead screw nut 6, frame 7, second-stage slide Block 8, first level slide bar 9 and second level guide rail 10;
[0015] There are two first-stage slider guide rails 2, leading screws 3, first-stage connecting rods 4, first-stage sliders 5, and leading screw nuts 6;
[0016] Two lead screws 3 are installed on both sides of the frame 7, and a lead screw nut 6 is respectively installed on the two lead screws 3;
[0017] Two first-level slider guide rails 2 are fixed on both sides of the frame 7 and are located directly below the lead screw 3; the two first-level slider guide rails 2 are parallel to the respective upper lead screw 3;
[0018] The two first-stage sliders 5 are respectively fixedly mounted on the lead screw nuts 6;
[0019] When the lead screw 3 rotates, the lead screw nut 6 drives the first-stage slid...
Embodiment 2
[0031] The device in this embodiment includes two sets of devices in Embodiment 1, the second-level connecting rod 11, the second-level sliding rod 12, the third-level sliding block 13 and the third-level guide rail 14;
[0032] The second-stage connecting rod 11, the second-stage slide bar 12, and the third-stage slide block 13 jointly constitute a coordinating rod device;
[0033] The third level slide block 13 is installed on the third level guide rail 14;
[0034] The second stage slide bar 12 passes through the third stage slide block 13, and the second stage slide bar 12 can slide along the axial direction of the second stage slide bar 12 relative to the third stage slide bar 13, and can also slide around the second stage. The axis of the rod 12 rotates, and the two form a cylindrical pair connection (when the installation plane of the two lead screws is parallel to the installation plane of the third-level guide rail 14, the second-level slide rod 12 and the third-level...
PUM
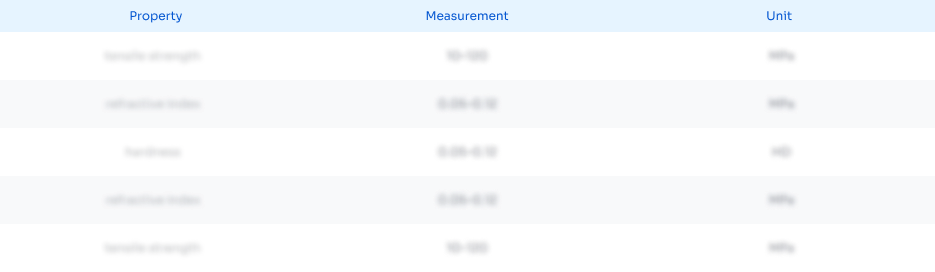
Abstract
Description
Claims
Application Information

- R&D Engineer
- R&D Manager
- IP Professional
- Industry Leading Data Capabilities
- Powerful AI technology
- Patent DNA Extraction
Browse by: Latest US Patents, China's latest patents, Technical Efficacy Thesaurus, Application Domain, Technology Topic, Popular Technical Reports.
© 2024 PatSnap. All rights reserved.Legal|Privacy policy|Modern Slavery Act Transparency Statement|Sitemap|About US| Contact US: help@patsnap.com