A kind of preparation method of light fastness and waterproof coating
A waterproof and light-resistant technology, applied in the direction of coating, etc., can solve the problems of poor quality, serious side effects and carcinogenicity, and achieve the effects of improving waterproof performance, improving hot stickiness, cold brittleness, and light resistance
- Summary
- Abstract
- Description
- Claims
- Application Information
AI Technical Summary
Problems solved by technology
Method used
Examples
example 1
[0020] (1) Add 67.5g of water, 0.5g of sodium dodecylbenzenesulfonate, 0.25g of fatty alcohol polyoxyethylene ether, and 0.45g of acrylic acid into a 500ml three-neck flask, raise the temperature to 45°C, stir for 45min, and add monomer A , emulsified for 40 minutes, heated up to 75°C, passed back flowing water, heated up to 80°C and kept warm, added dropwise 5.5g of azobisisobutylimidazoline hydrochloride solution dissolved in 5g of water, the dropwise addition time was 0.5h, and the dropwise reaction was completed for 2h , to obtain the core layer emulsion;
[0021] The A monomer is formed by mixing 7.5g of butyl acrylate, 4.5g of methyl methacrylate, 5.3g of ethyl acrylate, and 0.3g of styrene;
[0022] (2) Add B monomer and 4.5 g of azobisisobutylimidazoline hydrochloride solution dissolved in 4 g of water to the core layer emulsion obtained in step (1) at the same time, dropwise for 1 hour, and keep the reaction at 75°C for 2 hours. Add 1.5g of quercetin, heat at 75°C fo...
example 2
[0025] (1) Add 98g of water, 1.8g of sodium dodecylbenzenesulfonate, 0.9g of fatty alcohol polyoxyethylene ether, and 4.1g of acrylic acid into a 500ml three-necked flask, raise the temperature to 45°C, stir for 45min, add monomer A, Emulsify for 60 minutes, raise the temperature to 75°C, pass the reflux water, raise the temperature to 80°C, add dropwise 5.9g of tert-butyl peroxypivalate solution dissolved in 5g of water, dropwise for 2.5h, and react for 2h after the dropwise addition, to obtain the nucleus layer emulsion;
[0026] The A monomer is formed by mixing 10.5g of butyl acrylate, 7.5g of methyl methacrylate, 6.8g of ethyl acrylate and 0.9g of styrene;
[0027] (2) Add monomer B and 4.8 g of tert-butyl peroxypivalate solution dissolved in 4 g of water to the core layer emulsion obtained in step (1) at the same time, dropwise for 3 hours, keep warm at 85°C for 2 hours, and then Add 3g of gallic acid, heat at 85°C for 3 hours, add 1.5g of aluminum sulfate, adjust the p...
example 3
[0030] (1) Add 82.5g of water, 1.2g of sodium dodecylbenzenesulfonate, 0.6g of fatty alcohol polyoxyethylene ether, and 2.3g of acrylic acid into a 500ml three-neck flask, heat up to 45°C, stir for 45min, and add monomer A , emulsified for 50 minutes, raised the temperature to 75°C, passed reflux water, raised the temperature to 80°C, and added dropwise 5.7g of azobisisobutylimidazoline hydrochloride solution dissolved in 5g of water, and added dropwise for 1.5h, and reacted for 2h after the dropwise addition. Obtain the core layer emulsion;
[0031] The A monomer is formed by mixing 9 g of butyl acrylate, 6 g of methyl methacrylate, 6 g of ethyl acrylate, and 0.6 g of styrene;
[0032] (2) Add monomer B and 4.6 g of azobisisobutylimidazoline hydrochloride solution dissolved in 4 g of water to the core layer emulsion obtained in step (1) at the same time, drop for 2 hours, and keep the temperature at 80°C for 2 hours. Add 2.3g of rutin, keep it warm at 80°C for 2 hours, add 1...
PUM
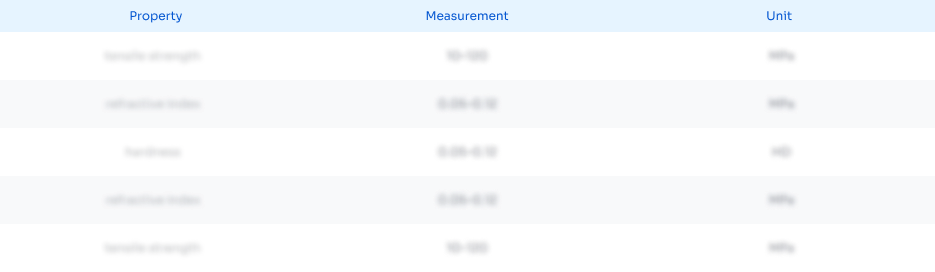
Abstract
Description
Claims
Application Information

- R&D Engineer
- R&D Manager
- IP Professional
- Industry Leading Data Capabilities
- Powerful AI technology
- Patent DNA Extraction
Browse by: Latest US Patents, China's latest patents, Technical Efficacy Thesaurus, Application Domain, Technology Topic, Popular Technical Reports.
© 2024 PatSnap. All rights reserved.Legal|Privacy policy|Modern Slavery Act Transparency Statement|Sitemap|About US| Contact US: help@patsnap.com