A kind of preparation method of flame-retardant core-shell type waterborne acrylic resin coating
A water-based acrylic and ester resin technology, used in fire-resistant coatings, coatings, etc., can solve the problem of halogen flame retardants burning large smoke and other problems, and achieve the effect of improving hot stickiness and cold brittleness
- Summary
- Abstract
- Description
- Claims
- Application Information
AI Technical Summary
Problems solved by technology
Method used
Examples
example 1
[0022] (1) Add 50g of water, 0.33g of emulsifier sodium dodecylbenzenesulfonate and fatty alcohol polyoxyethylene ether (the type of fatty alcohol polyoxyethylene ether is OS-15, non-ionic type, purchased from Jiangsu Haian Petrochemical Plant, the same below) 0.17g, methacrylic acid 0.3g, raise the reaction temperature to 40°C, stir for 15min, add A monomer, and emulsify for 30min. When the temperature rises to 70°C, flow back water, and when the temperature reaches 75°C, start to drop 5.2g of potassium persulfate solution dissolved in 5g of water, dropwise for 1h, keep warm for 3h, add dodecyltriphenylphosphonium chloride 1g, stirring reaction time 1h, to obtain the core layer emulsion;
[0023] A monomer and its dosage: A monomer is composed of 6g of butyl acrylate, 4g of methyl methacrylate, 2.5g of ethyl acrylate, and 3g of diborene;
[0024] (2) Add B monomer and 5.3g of potassium persulfate solution dissolved in 5g of water to the core layer emulsion at the same time, ...
example 2
[0027] (1) Add 70g of water, 1.2g of emulsifier sodium dodecylbenzenesulfonate, 0.6g of fatty alcohol polyoxyethylene ether, and 3.0g of methacrylic acid into a three-necked flask, raise the reaction temperature to 40°C, and stir for 15 minutes. Add A monomer, emulsification time 45min. When the temperature rises to 70°C, flow back water, and when the temperature reaches 75°C, start to drop 5.4g of ammonium persulfate solution dissolved in 5g of water, dropwise for 3h, keep stirring for 5h, add dedecyltriphenylphosphonium bromide 3g, stirring reaction time 3h, to obtain the core layer emulsion;
[0028] A monomer and its dosage: A monomer is composed of 8g of butyl acrylate, 6g of methyl methacrylate, 3.5g of ethyl acrylate and 6g of diborene;
[0029] (2) Add monomer B and 5.5g of ammonium persulfate solution dissolved in 5g of water dropwise to the core layer emulsion at the same time, dropwise for 3h, keep warm at 85°C for 2h, add 20g of m-carborane dropwise, keep warm and...
example 3
[0032] (1) Add 60g of water, 0.8g of emulsifier sodium dodecylbenzenesulfonate, 0.4g of fatty alcohol polyoxyethylene ether, and 1.7g of methacrylic acid into a three-necked flask, raise the reaction temperature to 40°C, and stir for 15 minutes. Add A monomer, and the emulsification time is 35min. When the temperature rises to 70°C, flow back water, and when the temperature reaches 75°C, dissolve 5.3g of potassium persulfate solution in 5g of water, add dropwise for 2h, keep stirring for 4h, add 2g of dodecyltriphenylphosphonium chloride, Stirring reaction time 2h, obtain core layer emulsion;
[0033] A monomer and its dosage: A monomer is composed of 7g of butyl acrylate, 5g of methyl methacrylate, 3.0g of ethyl acrylate and 4.5g of diborene;
[0034] (2) Add monomer B and 5.4g of potassium persulfate solution dissolved in 5g of water to the core emulsion at the same time, add dropwise for 2h, keep warm at 80°C for 2h, add 15g of triphenylborane dropwise, keep stirring Reac...
PUM
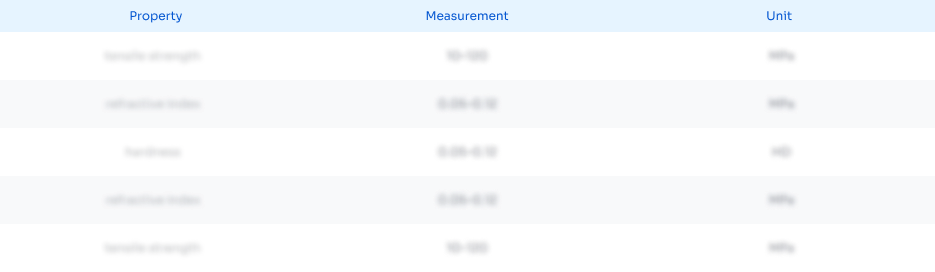
Abstract
Description
Claims
Application Information

- R&D Engineer
- R&D Manager
- IP Professional
- Industry Leading Data Capabilities
- Powerful AI technology
- Patent DNA Extraction
Browse by: Latest US Patents, China's latest patents, Technical Efficacy Thesaurus, Application Domain, Technology Topic, Popular Technical Reports.
© 2024 PatSnap. All rights reserved.Legal|Privacy policy|Modern Slavery Act Transparency Statement|Sitemap|About US| Contact US: help@patsnap.com