Multi-section reaming cast-in-place pile construction method
A construction method and cast-in-situ pile technology, which is applied to sheet pile walls, foundation structure engineering, construction, etc., can solve problems such as low construction efficiency, construction progress constraints, and complex hole-forming construction technology of extruded and expanded piles, so as to improve construction efficiency, The effect of ensuring the quality of piles
- Summary
- Abstract
- Description
- Claims
- Application Information
AI Technical Summary
Problems solved by technology
Method used
Image
Examples
Embodiment Construction
[0035] The construction method of multi-section drilled and expanded cast-in-situ piles according to the present invention is characterized in that it comprises the following operation steps:
[0036] ① Leveling the construction site, setting out pile positions and laying casings in sequence;
[0037] ②Centering and leveling the drilling rig in place: Move the drilling rig to the pile position, align the drill bit tip of the drilling rig expansion device with the center point of the pile position in the casing and level the frame so that the drill bit can be aligned on the pile position. Drilling holes are opened in the center; after the drilling rig is centered and leveled, the frame legs of the drilling rig or other contact parts with the ground should be stabilized and compacted to prevent the equipment from tilting or misaligning during the drilling construction process; A mud pool and a mud ditch are dug on one side;
[0038] ③ Drilling, multi-section reamin...
PUM
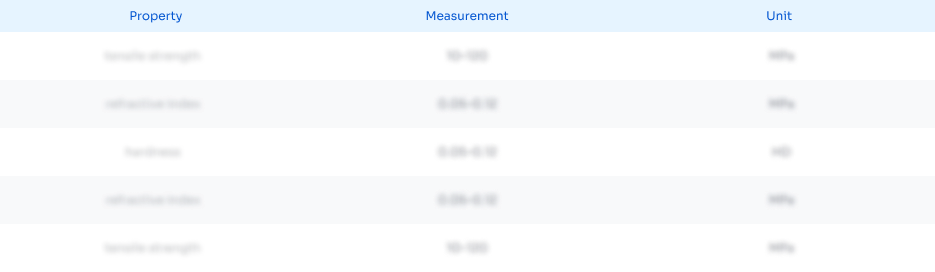
Abstract
Description
Claims
Application Information

- R&D Engineer
- R&D Manager
- IP Professional
- Industry Leading Data Capabilities
- Powerful AI technology
- Patent DNA Extraction
Browse by: Latest US Patents, China's latest patents, Technical Efficacy Thesaurus, Application Domain, Technology Topic, Popular Technical Reports.
© 2024 PatSnap. All rights reserved.Legal|Privacy policy|Modern Slavery Act Transparency Statement|Sitemap|About US| Contact US: help@patsnap.com