Cold-shrinkable foamed sleeve pipe, patterned sleeve pipe and preparation method thereof
The technology of sleeve and foaming agent is applied in the field of cold shrink sleeve and its preparation, which can solve problems such as sticking hands, and achieve the effects of improving production efficiency, reducing production cost and improving hand feeling.
- Summary
- Abstract
- Description
- Claims
- Application Information
AI Technical Summary
Problems solved by technology
Method used
Examples
Embodiment 1
[0029] (1) Preparation of rubber compound: in parts by weight, 100 parts of EPDM rubber, 10 parts of carbon black, 5 parts of calcined clay, 1 part of sulfur, 1 part of zinc oxide, 3 parts of azodicarbonamide (AC) 1 part and 1 part of zinc stearate are mixed on an open mill to form a uniform rubber compound;
[0030] (2) Extrude pipe: Extrude the compounded rubber through an extruder to form a pipe;
[0031] (3) Vulcanization and foaming to prepare foamed pipes: pre-vulcanize the mixed rubber at a temperature of 110-140°C for the first time, and then undergo secondary vulcanization and foaming at a temperature of 180-250°C to form foamed pipes;
[0032] (4) Expansion, cooling and shaping: expand the foamed pipe with expansion equipment at a temperature of 120-150 ° C, and cool and shape to form a cold-shrinkable foam sleeve.
Embodiment 2
[0034] (1) Preparation of rubber compound: in parts by weight, 100 parts of silicone rubber, 60 parts of white carbon black, 30 parts of calcined clay, 3 parts of vulcanizing agent bis-25, 5 parts of active zinc oxide, dinitrosopenta Mix 18 parts of methyltetramine (foaming agent H) on an internal mixer to form a uniform rubber compound;
[0035] (2) Extrude pipe: Extrude the compounded rubber through an extruder to form a pipe;
[0036] (3) Vulcanization and foaming to prepare foamed pipes: pre-vulcanize the mixed rubber at a temperature of 110-140°C for the first time, and then undergo secondary vulcanization and foaming at a temperature of 180-250°C to form foamed pipes;
[0037] (4) Expansion, cooling and shaping: expand the foamed pipe with expansion equipment at a temperature of 120-150 ° C, and cool and shape to form a cold-shrinkable foam sleeve.
Embodiment 3
[0039] (1) Preparation of rubber compound: by weight, 100 parts of EPDM rubber, 120 parts of carbon black, 6 parts of dicumyl peroxide (DCP), 5 parts of active zinc oxide, 4,4'~ Mix 35 parts of oxybis(benzenesulfonyl hydrazide) and 8 parts of calcium stearate on an open mixer or internal mixer to form a uniform rubber compound;
[0040] (2) Extrude pipe: Extrude the compounded rubber through an extruder to form a pipe;
[0041] (3) Vulcanization and foaming to prepare foamed pipes: pre-vulcanize the mixed rubber at a temperature of 110-140°C for the first time, and then undergo secondary vulcanization and foaming at a temperature of 180-250°C to form foamed pipes;
[0042] (4) Expansion, cooling and shaping: expand the foamed pipe with expansion equipment at a temperature of 120-150 ° C, and cool and shape to form a cold-shrinkable foam sleeve.
PUM
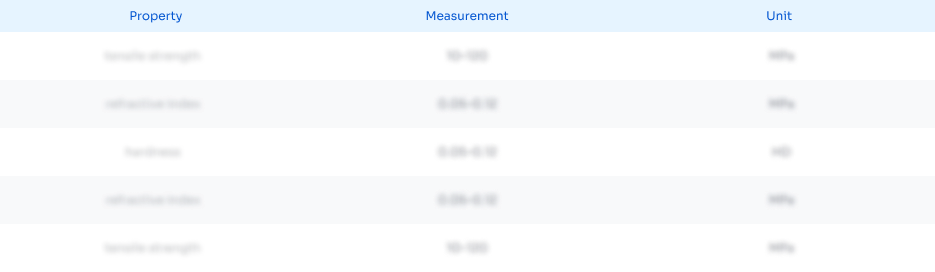
Abstract
Description
Claims
Application Information

- R&D
- Intellectual Property
- Life Sciences
- Materials
- Tech Scout
- Unparalleled Data Quality
- Higher Quality Content
- 60% Fewer Hallucinations
Browse by: Latest US Patents, China's latest patents, Technical Efficacy Thesaurus, Application Domain, Technology Topic, Popular Technical Reports.
© 2025 PatSnap. All rights reserved.Legal|Privacy policy|Modern Slavery Act Transparency Statement|Sitemap|About US| Contact US: help@patsnap.com