Supercritical water heat combustion reactor for thick oil injection production
A supercritical water and reactor technology, applied in the field of energy and environment, can solve the problems of high material consumption, slow oxidation reaction speed, environmental pollution, etc., to overcome the problems of coking and salt deposition, reduce the viscosity of heavy oil, and have a broad market prospect Effect
- Summary
- Abstract
- Description
- Claims
- Application Information
AI Technical Summary
Problems solved by technology
Method used
Image
Examples
Embodiment Construction
[0023] refer to Figure 1-Figure 5 , a supercritical hydrothermal combustion reactor for heavy oil injection and production, including an upper top cover 2 for bearing pressure, a reaction chamber 4 and a lower bottom cover 9, first nuts, bolts, gaskets 1 and 1 for sealing The second nut, bolt, gasket 10, and the first conical sealing surface 3 and the second conical sealing surface 8 are used to install the guide pipe 7 of the safety valve and pressure gauge, and the thermal insulation shell 11 for heat preservation is used for temperature measurement The first temperature measuring sleeve 5, the second temperature measuring sleeve 6 and the third temperature measuring sleeve 12~15, the annular groove 17 for introducing oxidant, the annular gap 16 for introducing supplementary water, and the upper top cover 2 The fuel inlet N5 arranged in the center, the thermocouple sockets N1~N4 arranged on the same circumference of the upper top cover 2 close to the fuel inlet N5, and the ...
PUM
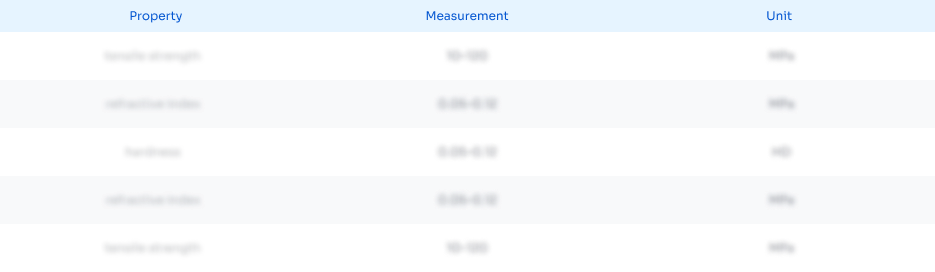
Abstract
Description
Claims
Application Information

- Generate Ideas
- Intellectual Property
- Life Sciences
- Materials
- Tech Scout
- Unparalleled Data Quality
- Higher Quality Content
- 60% Fewer Hallucinations
Browse by: Latest US Patents, China's latest patents, Technical Efficacy Thesaurus, Application Domain, Technology Topic, Popular Technical Reports.
© 2025 PatSnap. All rights reserved.Legal|Privacy policy|Modern Slavery Act Transparency Statement|Sitemap|About US| Contact US: help@patsnap.com