Partition machining method of triangular mesh model
A technology of triangular mesh and processing method, applied in the field of CAM, which can solve the problems of divide and conquer processing, inability to directly or effectively apply triangular mesh models, etc.
- Summary
- Abstract
- Description
- Claims
- Application Information
AI Technical Summary
Problems solved by technology
Method used
Image
Examples
Embodiment Construction
[0087] The present invention will be further described below in conjunction with drawings and embodiments.
[0088] Such as figure 1 As shown, the divide and conquer processing method of a triangular mesh model provided by the present invention specifically adopts the following steps:
[0089] Step 1. Read the triangular mesh model into memory, remove redundant vertices, and establish topology information based on the half-edge structure;
[0090] When reading the triangular mesh model, such as the STL model, from the hard disk into the memory, use the associated container classes in the C++ standard template library, such as set, map, multimap, etc., to remove redundant vertices and create a vector without repeated vertices Type point table and patch table; on this basis, also use the associated container class to create a half-edge data structure, the method is:
[0091] ① Take a triangular patch from the patch table, create three objects of the half-edge structure, and pr...
PUM
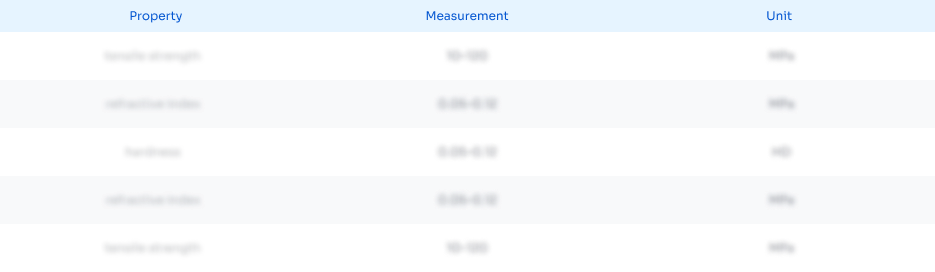
Abstract
Description
Claims
Application Information

- R&D
- Intellectual Property
- Life Sciences
- Materials
- Tech Scout
- Unparalleled Data Quality
- Higher Quality Content
- 60% Fewer Hallucinations
Browse by: Latest US Patents, China's latest patents, Technical Efficacy Thesaurus, Application Domain, Technology Topic, Popular Technical Reports.
© 2025 PatSnap. All rights reserved.Legal|Privacy policy|Modern Slavery Act Transparency Statement|Sitemap|About US| Contact US: help@patsnap.com