Inverse Emulsion Polymerization of High Solid Content and High Molecular Weight Anion Modified Polyacrylamide
An inverse emulsion polymerization and anion modification technology, which is applied in the direction of flocculation/sedimentation water/sewage treatment, etc., can solve the problems that the flocculation effect cannot be achieved, the molecular weight of the copolymer is not high, etc., and achieve the prevention of violent polymerization, the improvement of clarity, and the emulsion system stable effect
- Summary
- Abstract
- Description
- Claims
- Application Information
AI Technical Summary
Problems solved by technology
Method used
Examples
Embodiment 1
[0019] 1) Add 115 parts of deionized water to a 1000ml beaker, add 115 parts of pure acrylic acid (AA), and adjust PH=8.75 with about 182 parts of sodium hydroxide with a mass concentration of 35%. Activated carbon, which accounts for 10 wt% of sodium acrylate, was added to the solution, stirred at a constant temperature of 40 °C for 1 h, adsorbed the residual polymerization inhibitor in acrylic acid, filtered to obtain a pure sodium acrylate solution, and then 75 parts of refined acrylamide (AM) was dissolved in In pure sodium acrylate solution (SA), the AM / SA monomer solution is obtained.
[0020] 2) Into a 2000ml beaker, add 243.5 parts of 7# white oil, 15 parts of methyl glucoside sesquistearate and 30 parts of propylene glycol monostearate as an emulsifier (the total amount of emulsifier added accounts for the total amount of solvent). 6% by weight), dissolved and formulated into an oil phase. The oil phase was placed in a high shear mixer, and then the water phase was a...
Embodiment 2
[0025] 1) Add 115 parts of deionized water to a 1000ml beaker, add 115 parts of pure acrylic acid (AA), and adjust pH=8.55 with about 182 parts of sodium hydroxide with a mass concentration of 35%. Activated carbon, which accounts for 10 wt% of sodium acrylate, was added to the solution, stirred at a constant temperature of 40 °C for 1 h, adsorbed the residual polymerization inhibitor in acrylic acid, filtered to obtain a pure sodium acrylate solution, and then 75 parts of refined acrylamide (AM) was dissolved in In pure sodium acrylate solution (SA), the AM / SA monomer solution is obtained.
[0026] 2) To a 2000ml beaker, add 292.2 parts of 80# solvent oil, 15.5 parts of methyl glucoside sesquistearate and 31 parts of propylene glycol monostearate as emulsifier (the total amount of emulsifier added accounts for the total amount of solvent). 6% by weight), dissolved and formulated into an oil phase. The oil phase was placed in a high shear mixer, and then the water phase was a...
Embodiment 3
[0031] 1) Add 115 parts of deionized water to a 1000ml beaker, add 115 parts of pure acrylic acid (AA), and adjust pH=7.95 with about 182 parts of sodium hydroxide with a mass concentration of 35%. Activated carbon, which accounts for 10 wt% of sodium acrylate, was added to the solution, stirred at a constant temperature of 40 °C for 1 h, adsorbed the residual polymerization inhibitor in acrylic acid, filtered to obtain a pure sodium acrylate solution, and then 75 parts of refined acrylamide (AM) was dissolved in In pure sodium acrylate solution (SA), the AM / SA monomer solution is obtained.
[0032] 2) Into a 2000ml beaker, add 340.9 parts of 7# white oil, 37.5 parts of methyl glucoside sesquistearate and propylene glycol monostearate as emulsifier (the total amount of emulsifier added accounts for the total weight of the solvent; 10%), dissolved and formulated into an oil phase. The oil phase was placed in a high shear mixer, and then the water phase was added and emulsified...
PUM
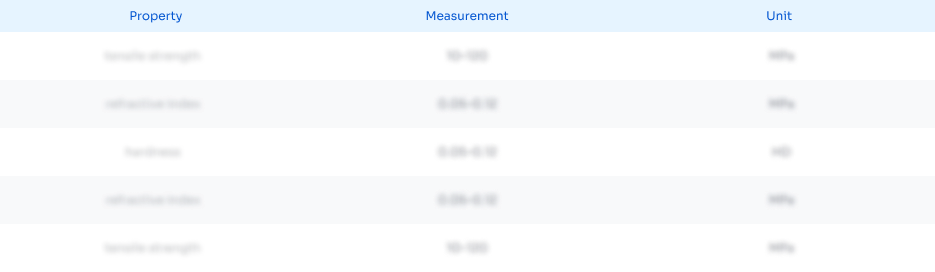
Abstract
Description
Claims
Application Information

- Generate Ideas
- Intellectual Property
- Life Sciences
- Materials
- Tech Scout
- Unparalleled Data Quality
- Higher Quality Content
- 60% Fewer Hallucinations
Browse by: Latest US Patents, China's latest patents, Technical Efficacy Thesaurus, Application Domain, Technology Topic, Popular Technical Reports.
© 2025 PatSnap. All rights reserved.Legal|Privacy policy|Modern Slavery Act Transparency Statement|Sitemap|About US| Contact US: help@patsnap.com