Blast-furnace casting runner
A technology for blast furnace tapping and blast furnace molten iron, which is applied in the direction of discharge device, etc., can solve the problems of skimmer burning and leakage, damage to the shape of the hole, affecting normal iron passing, etc., and achieves the effect of convenient dismantling and installation.
- Summary
- Abstract
- Description
- Claims
- Application Information
AI Technical Summary
Problems solved by technology
Method used
Image
Examples
Example Embodiment
[0022] The embodiments of the blast furnace tapping channel according to the present invention will be described below with reference to the drawings. Those of ordinary skill in the art can realize that the described embodiments can be modified in various ways without departing from the spirit and scope of the present invention. Therefore, the drawings and description are illustrative in nature, and are not used to limit the protection scope of the claims. In addition, in this specification, the same reference numerals indicate the same or similar parts.
[0023] figure 2 It is a perspective view showing the structure of a section of the blast furnace iron trough before installing the prefabricated skimmer according to an embodiment of the present invention, image 3 It is a perspective view showing the structure of a section of the blast furnace tapping channel after the prefabricated skimmer is installed according to an embodiment of the present invention, Figure 4a Is a cros...
PUM
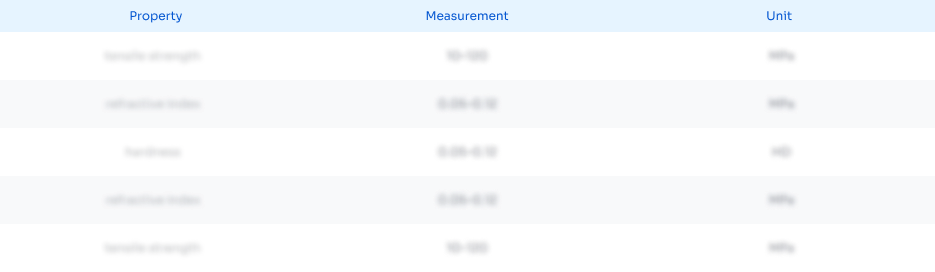
Abstract
Description
Claims
Application Information

- Generate Ideas
- Intellectual Property
- Life Sciences
- Materials
- Tech Scout
- Unparalleled Data Quality
- Higher Quality Content
- 60% Fewer Hallucinations
Browse by: Latest US Patents, China's latest patents, Technical Efficacy Thesaurus, Application Domain, Technology Topic, Popular Technical Reports.
© 2025 PatSnap. All rights reserved.Legal|Privacy policy|Modern Slavery Act Transparency Statement|Sitemap|About US| Contact US: help@patsnap.com