Robot system
A robot system and robot technology, applied in the field of robot systems, can solve the problems of not being able to monitor in real time, not being able to record welding construction data for a long time, and not considering multiple welding robots, etc.
- Summary
- Abstract
- Description
- Claims
- Application Information
AI Technical Summary
Problems solved by technology
Method used
Image
Examples
Embodiment Construction
[0035] Below, refer to Figure 1 to Figure 5 An embodiment in which the present invention is embodied as an arc welding robot system will be described.
[0036] like figure 1 As shown, the arc welding robot system 10 includes a plurality of robots (not shown) configured to perform arc welding, robot controllers RC1 , RC2 to RCN, and a monitoring device PC for controlling the robots.
[0037] The robots controlled by the robot controllers RC1 , RC2 to RCN are well-known articulated robots, so the description will be simplified. A manipulator constituting a robot is composed of a base member fixed to an appropriate place such as the ground, a plurality of arms connected to the base member via a plurality of joints, and a drive motor (not shown) that drives each arm. The drive motor includes a rotary encoder (not shown), and can detect the current position of the drive motor. A welding torch for arc welding a workpiece (not shown) as an object to be welded is attached to the d...
PUM
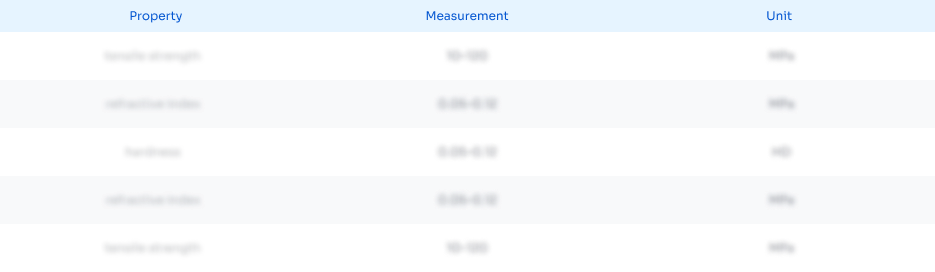
Abstract
Description
Claims
Application Information

- R&D
- Intellectual Property
- Life Sciences
- Materials
- Tech Scout
- Unparalleled Data Quality
- Higher Quality Content
- 60% Fewer Hallucinations
Browse by: Latest US Patents, China's latest patents, Technical Efficacy Thesaurus, Application Domain, Technology Topic, Popular Technical Reports.
© 2025 PatSnap. All rights reserved.Legal|Privacy policy|Modern Slavery Act Transparency Statement|Sitemap|About US| Contact US: help@patsnap.com