Method for extracting ferric phosphate from phosphorized waste residues
A technology of phosphating waste residue and iron phosphate, applied in chemical instruments and methods, phosphorus compounds, inorganic chemistry, etc., can solve problems such as environmental pollution, and achieve the effect of solving environmental pollution and improving economic benefits
- Summary
- Abstract
- Description
- Claims
- Application Information
AI Technical Summary
Problems solved by technology
Method used
Examples
Embodiment 1
[0019] One of the method that embodiment 1 extracts iron phosphate from phosphating waste residue
[0020] 1. Put the white powdery phosphating waste slag produced in the phosphating workshop into the reaction device, then add water, the weight ratio is phosphating waste slag: water = 1: 1, and stir evenly;
[0021] 2. Then slowly add concentrated hydrochloric acid to the reaction device until the white solid is completely dissolved;
[0022] 3. Filter the above solution with a sand core funnel; remove insoluble matter:
[0023] 4. Slowly add 2mol / L sodium hydroxide solution dropwise to the above filtrate, control the pH of the solution at 1.0, react for 3.5 hours, and filter with a sand core funnel;
[0024] 5. Take the filter cake, wash it with distilled water until it is neutral, and the pH is 6;
[0025] 6. Dry at 100° C. for 3 hours and crush to 300 mesh to obtain battery-grade ferric orthophosphate product.
Embodiment 2
[0026] Example 2 The second method of extracting iron phosphate from phosphating waste residue
[0027] 1. Put the white powdery phosphating waste residue produced in the phosphating workshop into the reaction device, then add water, the weight ratio is phosphating waste residue: water = 1: 1.2, and stir evenly;
[0028] 2. Then slowly add concentrated hydrochloric acid to the reaction device until the white solid is completely dissolved;
[0029] 3. Filter the above solution with a sand core funnel; remove insoluble matter;
[0030] 4. Slowly add 2mol / L sodium hydroxide solution dropwise to the above-mentioned filtrate, control the pH of the solution at 2.0, and after 2.5 hours of reaction, filter with a sand core funnel;
[0031] 5. Take the filter cake, wash it with distilled water until it is neutral, and the pH is 8;
[0032] 6. Dry at 110° C. for 2 hours, and crush to 300 mesh to obtain battery-grade ferric orthophosphate product.
PUM
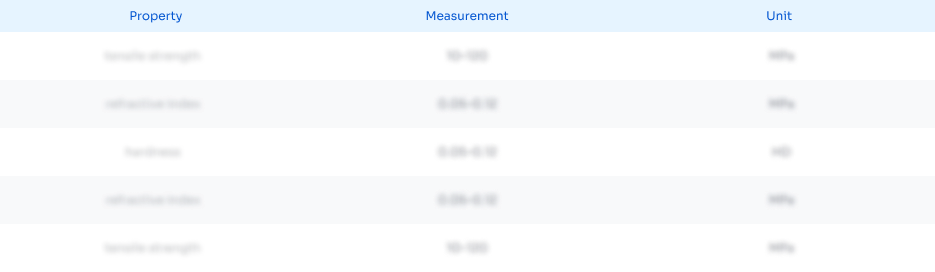
Abstract
Description
Claims
Application Information

- Generate Ideas
- Intellectual Property
- Life Sciences
- Materials
- Tech Scout
- Unparalleled Data Quality
- Higher Quality Content
- 60% Fewer Hallucinations
Browse by: Latest US Patents, China's latest patents, Technical Efficacy Thesaurus, Application Domain, Technology Topic, Popular Technical Reports.
© 2025 PatSnap. All rights reserved.Legal|Privacy policy|Modern Slavery Act Transparency Statement|Sitemap|About US| Contact US: help@patsnap.com