High-rigidity and light-weight sensitivity analysis method for passenger bus skeleton
A sensitivity analysis, high stiffness technology, applied in the field of high stiffness and lightweight sensitivity analysis of bus body frame, can solve problems such as large amount of calculation, calculation error, inability to reduce body mass, etc., to improve stiffness, reduce calculation amount, and reduce body weight quality effect
- Summary
- Abstract
- Description
- Claims
- Application Information
AI Technical Summary
Problems solved by technology
Method used
Image
Examples
Embodiment Construction
[0022] (1) Establish a parametric finite element model of the bus skeleton structure
[0023] figure 1 It is a box-section pipe, and the basic size parameters of its section are height h, width b, and thickness t. use figure 1 The Euler-Bernoul finite element beam element shown builds up figure 2 The finite element parametric model of the bus body skeleton is shown. The model simplifies the bus body and omits the skin structure. The model is divided into five major assemblies of front wall, rear wall, side wall, top cover and underframe, and is divided into 12 components in total. All beam elements in each component have the same cross-sectional size, so the body is a component parametric model.
[0024] In order to more accurately simulate the actual working conditions of the bus, the establishment image 3 Suspension model shown, assemble it on figure 2 In the vehicle model shown. A flexible beam structure is used to simulate the leaf spring, the width b of the beam...
PUM
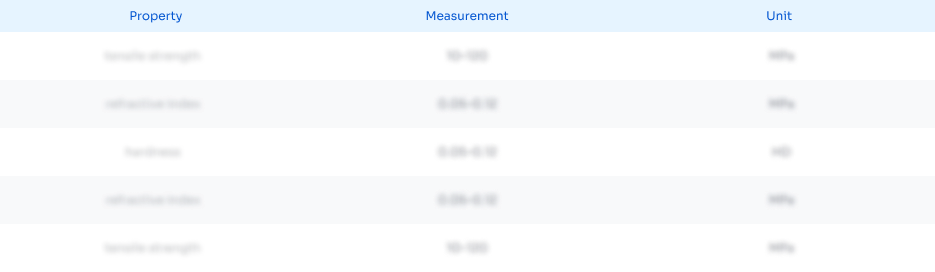
Abstract
Description
Claims
Application Information

- R&D Engineer
- R&D Manager
- IP Professional
- Industry Leading Data Capabilities
- Powerful AI technology
- Patent DNA Extraction
Browse by: Latest US Patents, China's latest patents, Technical Efficacy Thesaurus, Application Domain, Technology Topic, Popular Technical Reports.
© 2024 PatSnap. All rights reserved.Legal|Privacy policy|Modern Slavery Act Transparency Statement|Sitemap|About US| Contact US: help@patsnap.com