Method for preparing monopotassium phosphate by using wet-process phosphoric acid
A technology of potassium dihydrogen phosphate and wet-process phosphoric acid, applied in chemical instruments and methods, applications, phosphorus compounds, etc., can solve the problems of unstable product quality, difficult to handle by-products, long process lines, etc., to achieve stable product quality, The process route is short and the effect of overcoming the complex process
- Summary
- Abstract
- Description
- Claims
- Application Information
AI Technical Summary
Problems solved by technology
Method used
Image
Examples
Embodiment 1
[0042] (1) Impurity removal of wet-process phosphoric acid:
[0043] The solid impurities contained in the wet-process phosphoric acid with a concentration of 15% are removed by centrifugation or press filtration to obtain phosphoric acid for subsequent use;
[0044] (2) Synthesis reaction of intermediates:
[0045] Put the phosphoric acid obtained in step (1) into the intermediate synthesis tank, adjust the concentration of phosphoric acid, heat up to 60°C, and add carbonamide and phosphoric acid under stirring conditions to carry out the synthesis reaction. The amount of carbonamide added is based on the mole of phosphoric acid The ratio is 1.1:1 to determine, stirring to dissolve and heat preservation reaction, the reaction time is 80min;
[0046] (3) Cooling and crystallization to obtain the intermediate:
[0047] After the synthesis reaction is completed, put the obtained intermediate slurry into the cooling crystallization tank and cool it to a temperature of 20°C to c...
Embodiment 2
[0051] (1) Impurity removal of wet-process phosphoric acid:
[0052] The solid impurities contained in the wet-process phosphoric acid with a concentration of 40% are removed by centrifugation or press filtration to obtain phosphoric acid for subsequent use;
[0053] (2) Synthesis reaction of intermediates:
[0054] Put the phosphoric acid obtained in step (1) into the intermediate synthesis tank, adjust the concentration of phosphoric acid, heat up to 70°C, and add carbonamide and phosphoric acid under stirring conditions to carry out the synthesis reaction. The amount of carbonamide added is based on the mole of phosphoric acid The ratio is 1:1 to determine, stir to dissolve and keep warm for reaction, and the reaction time is 100min;
[0055] (3) Cooling and crystallization to obtain the intermediate:
[0056] After the synthesis reaction is completed, put the obtained intermediate slurry into the cooling crystallization tank to cool to a temperature of 30°C, centrifuge a...
Embodiment 3
[0060] (1) Impurity removal of wet-process phosphoric acid:
[0061] The solid impurities contained in the wet-process phosphoric acid with a concentration of 50% are removed by centrifugation or press filtration to obtain phosphoric acid for subsequent use;
[0062] (2) Synthesis reaction of intermediates:
[0063] Put the phosphoric acid obtained in step (1) into the intermediate synthesis tank, adjust the concentration of phosphoric acid, heat up to 80°C, and add carbonamide and phosphoric acid under stirring conditions to carry out the synthesis reaction. The amount of carbonamide added is based on the mole of phosphoric acid The ratio is 0.95:1 to determine, stirring to dissolve and heat preservation reaction, the reaction time is 60min;
[0064] (3) Cooling and crystallization to obtain the intermediate:
[0065] After the synthesis reaction is finished, put the obtained intermediate slurry into a cooling crystallization tank to cool to a temperature of 40°C, centrifug...
PUM
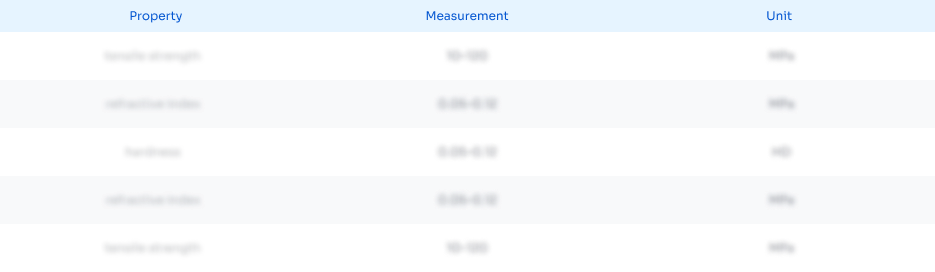
Abstract
Description
Claims
Application Information

- Generate Ideas
- Intellectual Property
- Life Sciences
- Materials
- Tech Scout
- Unparalleled Data Quality
- Higher Quality Content
- 60% Fewer Hallucinations
Browse by: Latest US Patents, China's latest patents, Technical Efficacy Thesaurus, Application Domain, Technology Topic, Popular Technical Reports.
© 2025 PatSnap. All rights reserved.Legal|Privacy policy|Modern Slavery Act Transparency Statement|Sitemap|About US| Contact US: help@patsnap.com