Temperature-self-compensating-integrated fiber bragg grating strain transducer and method for monitoring cable force of inhaul cable through integrated temperature self-compensating fiber bragg grating strain transducer
A technology of strain sensor and optical fiber grating, which is applied in the field of optical fiber grating technology, cable force sensor and a method for monitoring cable force, which can solve the problem of epoxy resin packaging exposed aging, strain and temperature cross sensitivity, optical fiber Brittle grating and other problems, to achieve the effect of novel structure, improved sensitivity, and improved sensitivity
- Summary
- Abstract
- Description
- Claims
- Application Information
AI Technical Summary
Problems solved by technology
Method used
Image
Examples
Embodiment 1
[0047] A fiber grating strain sensor with integrated temperature self-compensation, such as Figure 1 ~ Figure 3 As shown, the integrated temperature self-compensating fiber grating strain sensor includes a fiber grating sensor 1, a shrapnel 2, a clamping part 3, a base 4, a Z-shaped movable part 5 and a frame 6;
[0048] The fiber grating sensor 1 is composed of two bare fiber gratings 101, 102 of the same model and different wave bands;
[0049] The shrapnel 2 is a high-elastic metal sheet designed as an equal-strength beam;
[0050] There are two clamping parts 3, which are metal squares with two through holes;
[0051] The base 4 has 2 pieces, which are square metal plates, and the upper end of the base has an open square groove for placing the connecting shaft of the Z-shaped movable part 5 or the connecting shaft of the frame 6; The threaded hole for installing the clamping piece 3; there is a mounting hole for fixing the base on the tested piece on each symmetrical si...
Embodiment 2
[0065] A method for monitoring the force of a cable, which is a method for monitoring the force of a cable using the fiber grating strain sensor described in Embodiment 1. The specific method is: prepare the required number of integrated temperature self-compensating fiber grating strain sensors , supporting measuring equipment 10 and connecting wire; the gauge distance of the surface to be measured at the cable anchor cup 8 to be measured; the 2 bases 4 of the fiber grating strain sensor with integrated temperature self-compensation are removed, and the 2 bases 4 are Screws are bolted or welded to the two ends of the gauge length of the surface of the anchor cup, and then the rest of the fiber grating strain sensor with integrated temperature self-compensation is re-clamped on the base 4; A fiber grating strain sensor with integrated temperature self-compensation is deployed to the Figure 5 , Figure 6 ); After the connection is completed, turn on the measuring equipment to...
PUM
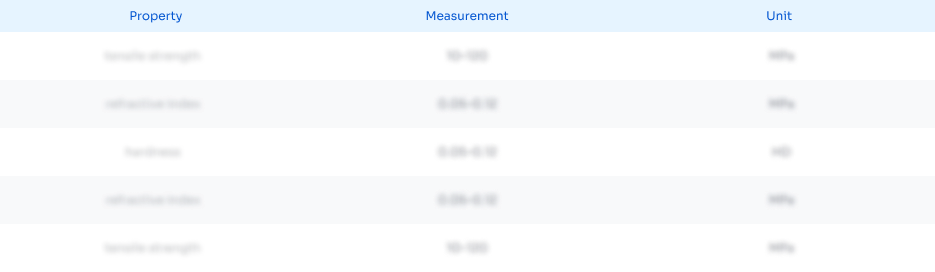
Abstract
Description
Claims
Application Information

- R&D Engineer
- R&D Manager
- IP Professional
- Industry Leading Data Capabilities
- Powerful AI technology
- Patent DNA Extraction
Browse by: Latest US Patents, China's latest patents, Technical Efficacy Thesaurus, Application Domain, Technology Topic, Popular Technical Reports.
© 2024 PatSnap. All rights reserved.Legal|Privacy policy|Modern Slavery Act Transparency Statement|Sitemap|About US| Contact US: help@patsnap.com