A kind of preparation method of methyl tert-amyl ether
A technology of methyl tert-amyl ether and methyl butene, which is applied in the field of preparation of methyl tert-amyl ether, can solve the problems of increased by-products, easy detachment of sulfonic acid groups, and corrosion of equipment, so as to improve the conversion of olefins High efficiency, inhibition of side effects, good stability
- Summary
- Abstract
- Description
- Claims
- Application Information
AI Technical Summary
Problems solved by technology
Method used
Examples
preparation example Construction
[0030] In the preparation process of the above-mentioned aluminum-based composite oxide, the reaction time is 2h-20h, preferably 4h-16h, most preferably 6h-12h. The drying temperature is 90°C-150°C, preferably 100°C-140°C, most preferably 110°C-130°C. The drying time is 4h-24h, preferably 6h-16h, most preferably 10h-12h. The calcination temperature is 400°C-800°C, preferably 450°C-700°C, most preferably 500°C-600°C. The calcination time is 8h-24h, preferably 8h-14h, most preferably 8h-12h.
[0031] The formed aluminum-based composite oxide support is impregnated in a heteropolyacid solution according to a conventional impregnation method. The immersion time is 4h-24h, preferably 4h-12h, most preferably 6h-12h. The impregnation is dried at 100°C-180°C for 4h-12h, preferably at 100°C-160°C for 6h-12h, most preferably at 100°C-120°C for 6h-8h. The impregnation is calcined at 250°C-550°C for 6h-24h, preferably at 300°C-500°C for 6h-12h, most preferably at 350°C-450°C for 8h-12...
Embodiment 1
[0034] A certain amount of aluminum nitrate and a certain amount of magnesium nitrate are prepared into an aqueous solution a, and deionized water and a certain amount of potassium hydroxide are used to prepare an aqueous solution b, and the solution b is added dropwise to a under normal temperature and stirring, and the reaction After 6 hours, a white paste precipitate was obtained, which was washed, filtered, and dried at 120°C for 10 hours, then extruded according to a conventional method, and then calcined at 500°C for 8 hours to obtain a magnesium-aluminum composite oxide carrier.
[0035] Dissolve phosphomolybdic acid in deionized water, immerse the above-mentioned shaped and roasted catalyst carrier in the heteropoly solution for 12 hours, dry the impregnated material at 110°C for 12 hours, and roast at 350°C for 8 hours to obtain the catalyst. The catalyst composition is shown in Table 1.
[0036] The etherification of 2-methylbutene and methanol is carried out in a Φ1...
Embodiment 2
[0038] Other conditions are the same as in Example 1, except that the consumption of magnesium nitrate and phosphomolybdic acid is changed, the catalyst composition is shown in Table 1, and the reaction results are shown in Table 2.
PUM
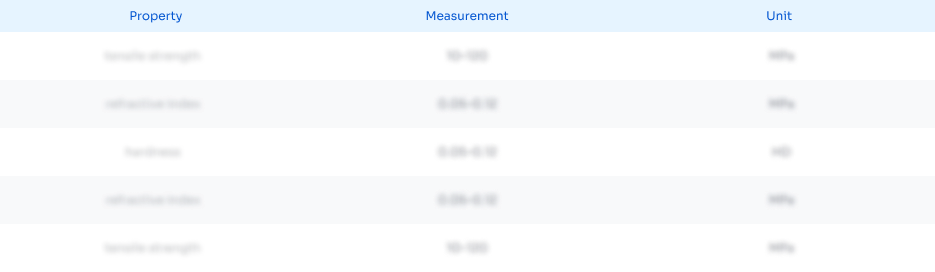
Abstract
Description
Claims
Application Information

- R&D
- Intellectual Property
- Life Sciences
- Materials
- Tech Scout
- Unparalleled Data Quality
- Higher Quality Content
- 60% Fewer Hallucinations
Browse by: Latest US Patents, China's latest patents, Technical Efficacy Thesaurus, Application Domain, Technology Topic, Popular Technical Reports.
© 2025 PatSnap. All rights reserved.Legal|Privacy policy|Modern Slavery Act Transparency Statement|Sitemap|About US| Contact US: help@patsnap.com