Ship-based heavy stabilizing platform
A stabilized platform, heavy-duty technology, applied in the structural design of stabilized platforms, shipborne heavy-duty stabilized platforms, can solve the problems of small load capacity, inability to achieve stability, high delay, etc., to improve stability accuracy, improve structural strength, and load powerful effect
- Summary
- Abstract
- Description
- Claims
- Application Information
AI Technical Summary
Problems solved by technology
Method used
Image
Examples
Embodiment Construction
[0032] The specific implementation of the present invention will be further described below in conjunction with the accompanying drawings and examples. The following examples are only used to illustrate the technical solutions of the present invention more clearly, but not to limit the protection scope of the present invention.
[0033] Such as Figure 1 to Figure 9 As shown, the technical solution of the present invention is a ship-borne heavy-duty stable platform, including a main bracket 1, an installation platform 2, an inner frame 3, a roll servo reduction motor 4, a servo control box 5, and a pitch servo reduction motor 6 , gyro board 7, gyro A8, gyro B9, angle sensor A10, angle sensor B11, inclination sensor 12, inner ring shaft A13, inner ring shaft B14, inner ring gear 15, inner ring servo motor gear 16, outer ring shaft 17, Gear shaft 18, outer ring servo motor gear 19, motor bracket 20;
[0034] Wherein, the main bracket 1 includes a chassis 1-1 and a support ring;...
PUM
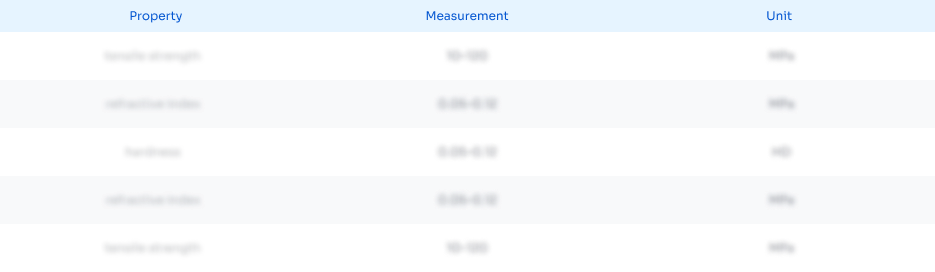
Abstract
Description
Claims
Application Information

- R&D
- Intellectual Property
- Life Sciences
- Materials
- Tech Scout
- Unparalleled Data Quality
- Higher Quality Content
- 60% Fewer Hallucinations
Browse by: Latest US Patents, China's latest patents, Technical Efficacy Thesaurus, Application Domain, Technology Topic, Popular Technical Reports.
© 2025 PatSnap. All rights reserved.Legal|Privacy policy|Modern Slavery Act Transparency Statement|Sitemap|About US| Contact US: help@patsnap.com