Belt pulley runout detecting tool
A technology of jump detection and pulley, which is applied in the direction of measuring device, mechanical measuring device, and mechanical device, etc., can solve the problems of large size error of pulley, reduced belt life, skewed groove shape of pulley, etc., so as to ensure the use effect and The effect of longer life, increased sampling ratio, and low manufacturing cost
- Summary
- Abstract
- Description
- Claims
- Application Information
AI Technical Summary
Problems solved by technology
Method used
Image
Examples
Embodiment 1
[0013] Example 1: Reference Figures 1 to 3 . A pulley runout detection tool includes several dial indicators, a base 12, a fixed seat 3, a screw rod 5, a handwheel 1, a sliding seat 6, a positioning shaft 8, a guide shaft 14, a floating bracket 15, and a fixed bracket 16. A fixing bracket 16 is arranged on the left side above the seat 12, and a fixing seat 3 is arranged on the right side. The fixing seat 3 is provided with a chute 31 with an upward opening. 5. The left end is connected to the left groove wall of the fixed seat 3, and its right end protrudes from the right groove wall of the fixed seat 3 and is connected to the center of the handwheel 1 outside the right end of the fixed seat 3. The lower end of the sliding seat 6 extends into the chute 31 and It is connected with the horizontal guide of the screw 5, and the front and rear sides of the lower end of the sliding seat 6 are respectively connected with the front and rear groove walls of the chute 31. The upper en...
PUM
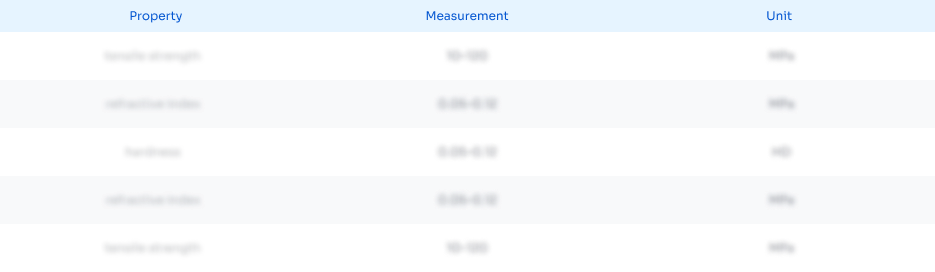
Abstract
Description
Claims
Application Information

- R&D
- Intellectual Property
- Life Sciences
- Materials
- Tech Scout
- Unparalleled Data Quality
- Higher Quality Content
- 60% Fewer Hallucinations
Browse by: Latest US Patents, China's latest patents, Technical Efficacy Thesaurus, Application Domain, Technology Topic, Popular Technical Reports.
© 2025 PatSnap. All rights reserved.Legal|Privacy policy|Modern Slavery Act Transparency Statement|Sitemap|About US| Contact US: help@patsnap.com