Design method for dreg slide plate curved surface of heading machine cutter head
A design method and ballast board technology, which are used in mining equipment, earth-moving drilling, tunnels, etc., can solve problems such as insufficient ballast removal, and achieve the effects of optimizing sliding trajectory, reducing vibration and improving strength.
- Summary
- Abstract
- Description
- Claims
- Application Information
AI Technical Summary
Problems solved by technology
Method used
Image
Examples
Embodiment Construction
[0021] The specific implementation of the present invention will be described in detail in conjunction with the accompanying drawings and technical solutions. During the working process of the roadheader, the scraper is arranged around the cutterhead, and the rock crushed by the hob falls to the bottom of the cutterhead by its own weight. When the scraper passes through the bottom of the cutterhead, it will blow up this part of the rock After the ballast is blown up, the rock ballast will fall onto the ballast slide plate, and the rock ballast will gradually overcome the friction between the ballast slide plate and the ballast slide plate during the rotation of the cutter head, and then fall along the ballast slide plate to the belt conveyor for discharge.
[0022] The ballast discharge system of the roadheader has an important impact on the overall work efficiency. If the rock ballast cannot be discharged from the cutter head in time, the roadheader will not be able to continu...
PUM
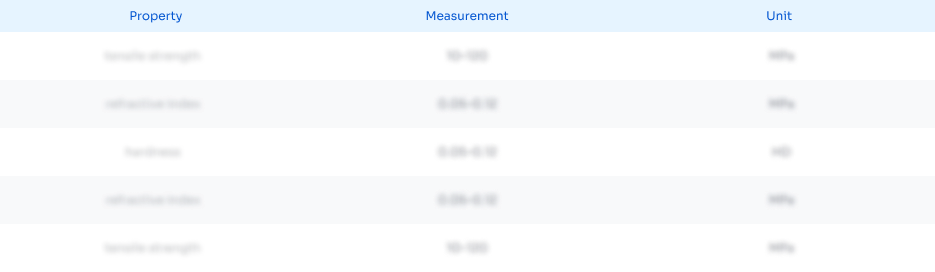
Abstract
Description
Claims
Application Information

- R&D
- Intellectual Property
- Life Sciences
- Materials
- Tech Scout
- Unparalleled Data Quality
- Higher Quality Content
- 60% Fewer Hallucinations
Browse by: Latest US Patents, China's latest patents, Technical Efficacy Thesaurus, Application Domain, Technology Topic, Popular Technical Reports.
© 2025 PatSnap. All rights reserved.Legal|Privacy policy|Modern Slavery Act Transparency Statement|Sitemap|About US| Contact US: help@patsnap.com