Modified silicate waterborne zinc-rich anticorrosive coating employing organic montmorillonite as anti-settling dispersant
An organic montmorillonite, anti-corrosion coating technology, applied in anti-corrosion coatings, coatings and other directions, can solve the problems of uneven gloss of zinc-based coatings, reduced corrosion resistance, easy to agglomerate, etc., to achieve excellent adhesion, The effect of fineness improvement and improved protective performance
- Summary
- Abstract
- Description
- Claims
- Application Information
AI Technical Summary
Problems solved by technology
Method used
Examples
Embodiment 1
[0029] 1) Weigh 17.4g of flaky zinc powder according to the formula ratio to obtain component A. The flaky zinc powder is superfine zinc powder, the effective zinc content of zinc powder is 96%, and the fineness is 500 mesh;
[0030] 2) Preparation of potassium silicate solution modified by silicon-acrylic emulsion: Weigh silica sol, potassium hydroxide and water with a mass ratio of 11.27:1:7.63, add silica sol to a constant temperature container with an electric stirrer, and At a constant temperature of 70°C, slowly add potassium hydroxide and water into the reaction container while stirring, and stir the mixed solution for 10 minutes to obtain a potassium silicate solution. Weigh the potassium silicate solution into a constant temperature container, , while stirring, a certain proportion of silicon-acrylic emulsion will be added, and after electric stirring for 40 minutes, the modified base material will be obtained. 2 :K 2 O is 5.5;
[0031] 3) Weigh 52g of emulsion-modi...
Embodiment 2
[0040] 1) Weigh 19.7g of zinc powder according to the formula ratio to obtain component A. The flaky zinc powder is ultrafine zinc powder, the effective zinc content of zinc powder is 96%, and the fineness is 500 mesh;
[0041] 2) Preparation of potassium silicate solution modified by silicon-acrylic emulsion: Weigh silica sol, potassium hydroxide and water with a mass ratio of 11.27:1:7.63, add silica sol to a constant temperature container with an electric stirrer, and At a constant temperature of 70°C, slowly add potassium hydroxide and water into the reaction vessel while stirring, and stir the mixed solution for about 10 minutes to obtain a potassium silicate solution. Next, while stirring, a certain proportion of silicon-acrylic emulsion will be added, and after electric stirring for 40 minutes, the modified base material will be obtained, wherein the mass fraction of silicon-acrylic emulsion is controlled to be 20%, and the molar ratio of silicon to potassium to SiO 2 :...
Embodiment 3
[0049] 1) Weigh 20g of zinc powder according to the formula ratio to obtain component A. The flaky zinc powder is superfine zinc powder, the effective zinc content of zinc powder is 97%, and the fineness is 500 mesh;
[0050] 2) Preparation of potassium silicate solution modified by silicon-acrylic emulsion: Weigh silica sol, potassium hydroxide and water with a mass ratio of 4.12:1:7.63, add silica sol to a constant temperature container with an electric stirrer, and At a constant temperature of 70°C, slowly add potassium hydroxide and water into the reaction vessel while stirring, and stir the mixed solution for about 10 minutes to obtain a potassium silicate solution. Next, while stirring, a certain proportion of silicon-acrylic emulsion will be added, and after electric stirring for 40 minutes, the modified base material will be obtained, wherein the mass fraction of silicon-acrylic emulsion is controlled to be 20%, and the molar ratio of silicon to potassium to SiO 2 :K ...
PUM
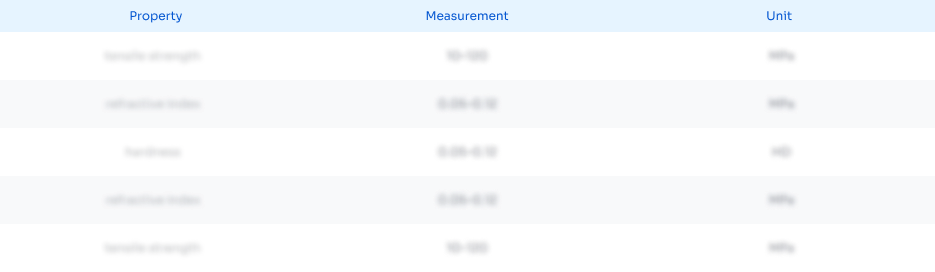
Abstract
Description
Claims
Application Information

- Generate Ideas
- Intellectual Property
- Life Sciences
- Materials
- Tech Scout
- Unparalleled Data Quality
- Higher Quality Content
- 60% Fewer Hallucinations
Browse by: Latest US Patents, China's latest patents, Technical Efficacy Thesaurus, Application Domain, Technology Topic, Popular Technical Reports.
© 2025 PatSnap. All rights reserved.Legal|Privacy policy|Modern Slavery Act Transparency Statement|Sitemap|About US| Contact US: help@patsnap.com