Flattening mould with cooling cycle system
A circulation system and mold technology, applied in the field of stamping molds, can solve the problems of reduced service life and production efficiency of molds and parts, heat generation of punches and products, and difficult maintenance, so as to reduce thermal deformation and springback effects, reduce The probability of water leakage and failure, and the effect of improving the stability of flattened thickness
- Summary
- Abstract
- Description
- Claims
- Application Information
AI Technical Summary
Problems solved by technology
Method used
Image
Examples
Embodiment Construction
[0017] In order to allow those skilled in the art to better understand the technical solutions of the present invention, the present invention will be further described below in conjunction with the accompanying drawings.
[0018] Such as figure 1 As shown, a flattening die with a cooling circulation system includes an upper die base 1 connected to a slide on the punch press, a lower die base 10 installed on the punch workbench, a punch fixing plate 3 below the upper die base 1, Punch fixing plate backing plate 2 between upper die base 1 and punch fixing plate 3, unloading plate 6 under punch fixing plate 3, unloading plate pad between punch fixing plate 3 and unloading plate 6 Plate 4, the flat punch 5 fixed on the punch fixing plate 3, the concave template 8 above the lower mold base 1 and the concave template backing plate 9 between the concave template 8 and the lower mold base 10, the discharge plate 6 A discharge plate insert 7 is provided inside, and a water circulatio...
PUM
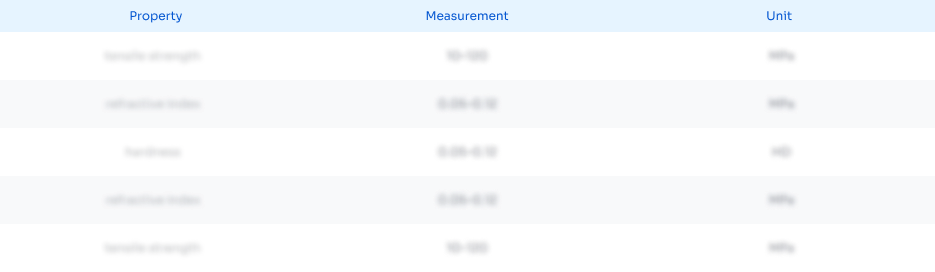
Abstract
Description
Claims
Application Information

- R&D
- Intellectual Property
- Life Sciences
- Materials
- Tech Scout
- Unparalleled Data Quality
- Higher Quality Content
- 60% Fewer Hallucinations
Browse by: Latest US Patents, China's latest patents, Technical Efficacy Thesaurus, Application Domain, Technology Topic, Popular Technical Reports.
© 2025 PatSnap. All rights reserved.Legal|Privacy policy|Modern Slavery Act Transparency Statement|Sitemap|About US| Contact US: help@patsnap.com