Modified polyurethane spraying composite material for cold insulation of ultralow temperature liquefied natural gas (LNG) storage tank and preparation method of composite material
A polyurethane, ultra-low temperature technology, used in polyurea/polyurethane coatings, coatings, etc., can solve the problems of poor dimensional stability of pore pressure difference materials, easy to produce shrinkage cracks, unable to ensure safety and normal use status, etc. The method is convenient and efficient, the effect of high pore pressure difference and dimensional stability, and excellent low temperature dimensional stability
- Summary
- Abstract
- Description
- Claims
- Application Information
AI Technical Summary
Problems solved by technology
Method used
Image
Examples
Embodiment 1
[0029] 1. Preparation of component A, 200kg: Weigh polyether polyol A: 450L (Shandong Bluestar Dongda Company), 76kg, polyether polyol B: DZ102C (Shandong Zibo Nuoli Chemical Co., Ltd.), 20kg, special Polyester polyol: TE-B503 (produced by our company), 17kg, foam stabilizer A: B-8545 (Evonik), 1kg, foam stabilizer B: LK-443 (Air Chemical), 2kg, deionized Water, 1.1kg, catalyst selection N,N,N',N",N"-pentamethyldiethylenetriamine, triethylenediamine, 1,3,5-tris(dimethylaminopropyl)- Mixture of hexahydrotriazine and dibutyltin dilaurate, weighing 1.5kg, 0.8kg, 0.4kg and 0.2kg respectively, physical blowing agent monofluorodichloroethane (141b), 40kg, flame retardant TCPP, 36kg , green pulp, 4kg.
[0030] The weighed polyether polyol A, polyether polyol B, special polyester polyol, foam stabilizer A, foam stabilizer B, chemical foaming agent, catalyst, flame retardant, physical foaming agent and others Add additives to the reaction kettle in turn, stir at room temperature for ...
Embodiment 2
[0034] 1. Prepare component A, 200kg: Weigh polyether polyol A: 450L (Shandong Bluestar Dongda Company), 60kg, polyether polyol B: DZ102C (Shandong Zibo Nuoli Chemical Co., Ltd.), 36kg, special Polyester polyol: TE-B503 (produced by our company), 20kg, foam stabilizer A: B-8545 (Evonik), 1kg, foam stabilizer B: LK-443 (Air Chemical), 2kg, deionized Water, 2kg, catalyst selection N,N,N',N",N"-pentamethyldiethylenetriamine, 1,3,5-tris(dimethylaminopropyl)-hexahydrotriazine and di Mixture of dibutyltin laurate, weighing 1.6kg, 1.0kg and 0.4kg respectively, physical foaming agent monofluorodichloroethane (141b), 40kg, flame retardant APP (ammonium polyphosphate), 32kg, antioxidant , 1kg, green pulp, 3kg.
[0035] The weighed polyether polyol A, polyether polyol B, special polyester polyol, foam stabilizer A, foam stabilizer B, chemical foaming agent, catalyst, flame retardant, physical foaming agent and others Add additives to the reaction kettle in turn, stir at room temperatur...
Embodiment 3
[0039] 1. Preparation of component A, 200kg: Weigh polyether polyol A: 450L (Shandong Bluestar Dongda Company), 75kg, polyether polyol B: DZ102C (Shandong Zibo Nuoli Chemical Co., Ltd.), 35kg, special Polyester polyol: B503 (produced by our company), 20kg, foam stabilizer A: B8532 (Evonik), 1kg, foam stabilizer B: LK-443 (Air Chemical), 2kg, deionized water, 1.8kg , The catalyst is selected from N,N,N',N",N"-pentamethyldiethylenetriamine, triethylenediamine, 1,3,5-tris(dimethylaminopropyl)-hexahydrotriazine and dibutyltin dilaurate, the weights are 1.3kg, 1.1kg, 0.5kg and 0.1kg respectively, the physical foaming agent fluorodichloroethane (141b), 25kg, flame retardant TCPP20kg, flame retardant DMMP15kg, Antioxidant, 2.2kg.
[0040]The weighed polyether polyol A, polyether polyol B, special polyester polyol, foam stabilizer A, foam stabilizer B, chemical foaming agent, catalyst, flame retardant, physical foaming agent and others Add additives to the reaction kettle in turn, s...
PUM
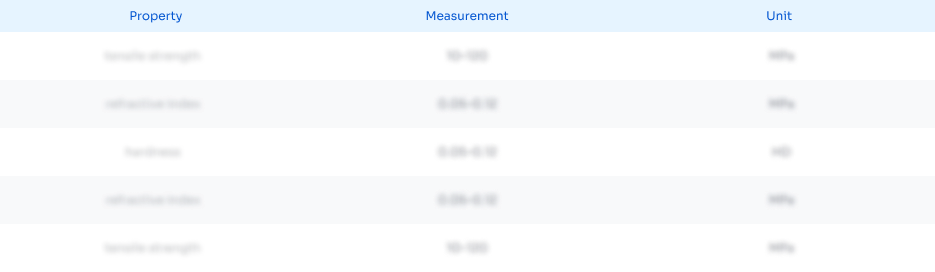
Abstract
Description
Claims
Application Information

- R&D
- Intellectual Property
- Life Sciences
- Materials
- Tech Scout
- Unparalleled Data Quality
- Higher Quality Content
- 60% Fewer Hallucinations
Browse by: Latest US Patents, China's latest patents, Technical Efficacy Thesaurus, Application Domain, Technology Topic, Popular Technical Reports.
© 2025 PatSnap. All rights reserved.Legal|Privacy policy|Modern Slavery Act Transparency Statement|Sitemap|About US| Contact US: help@patsnap.com