Wireless passive high-temperature pressure sensor with temperature compensation and temperature compensation algorithm thereof
A pressure sensor and temperature compensation technology, which is applied in the direction of fluid pressure measurement, fluid pressure measurement, and instrument using capacitance change, which can solve the problem that pressure sensors cannot measure pressure, and achieve the effect of ingenious design, low cost and reasonable structure.
- Summary
- Abstract
- Description
- Claims
- Application Information
AI Technical Summary
Problems solved by technology
Method used
Image
Examples
Embodiment Construction
[0021] A wireless passive high-temperature pressure sensor with temperature compensation, including a first green chip 1, a second green chip 2, a third green chip 3, a fourth green chip 4, and a fifth green chip 5;
[0022] The first green ceramic sheet 1, the second green ceramic sheet 2, the third green ceramic sheet 3, the fourth green ceramic sheet 4, and the fifth green ceramic sheet 5 are sequentially stacked into one body from bottom to top;
[0023] The lower pole plate 6 of the first flat capacitor is arranged on the left part of the upper surface of the first green ceramic sheet 1; the lower pole plate 7 of the second flat capacitor is arranged on the right part of the upper surface of the first green ceramic sheet 1; The left rear portion of the sheet 1 is provided with a first vent hole 8 penetrating up and down; the right rear portion of the first green ceramic sheet 1 is provided with a second vent hole 9 penetrating up and down; the opening of the second vent ho...
PUM
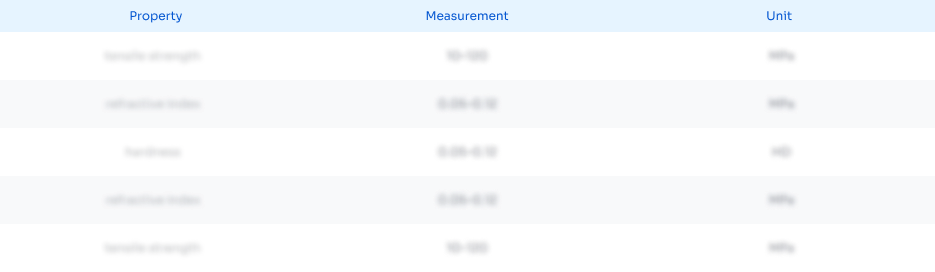
Abstract
Description
Claims
Application Information

- R&D
- Intellectual Property
- Life Sciences
- Materials
- Tech Scout
- Unparalleled Data Quality
- Higher Quality Content
- 60% Fewer Hallucinations
Browse by: Latest US Patents, China's latest patents, Technical Efficacy Thesaurus, Application Domain, Technology Topic, Popular Technical Reports.
© 2025 PatSnap. All rights reserved.Legal|Privacy policy|Modern Slavery Act Transparency Statement|Sitemap|About US| Contact US: help@patsnap.com