Connecting rod of sewing machine and preparation method thereof
A sewing machine and connecting rod technology, which is applied to sewing machine components, needle holders for sewing machines, sewing equipment, etc., can solve the problems affecting the development of the garment industry, poor quality assurance of processing, and poor quality of sewing machine connecting rods, etc., and achieves easy mechanization and automation. , low cost and high production efficiency
- Summary
- Abstract
- Description
- Claims
- Application Information
AI Technical Summary
Problems solved by technology
Method used
Image
Examples
Embodiment 1
[0036] According to the composition and mass percentage of Example 1 in Table 1, first add half of the aluminum ingot, heat it to 660°C to completely melt the aluminum ingot, then add silicon, copper and the remaining aluminum ingot, and wait until the silicon and copper are completely melted. Add nickel and zinc, adjust the temperature of the aluminum alloy liquid to 700℃, press into the magnesium flakes with a bell jar, after the magnesium is completely melted, stir the molten aluminum alloy liquid evenly, and let it stand for 5 minutes before slagging. Then, scandium is pressed into the aluminum alloy liquid, and after the scandium is completely melted, the aluminum alloy liquid is subjected to slag removal and degassing refining. After that, the processed aluminum alloy liquid is punched and die-cast under the condition of a pressure of 90 MPa to obtain needle bar crankshaft rod blanks, needle bar column blanks and needle bar holding parts blanks. Then, the needle bar crank...
Embodiment 2
[0038] According to the composition of Example 2 in Table 1 and its mass percentage, first add half of the aluminum ingot, heat to 680°C to completely melt the aluminum ingot, then add silicon, copper and the remaining aluminum ingot, and wait until the silicon and copper are completely melted. Add nickel and zinc, adjust the temperature of the aluminum alloy liquid to 710℃, press into the magnesium flakes with a bell jar, after the magnesium is completely melted, stir the molten aluminum alloy liquid evenly, and let it stand for 8 minutes before slagging. Then, scandium is pressed into the aluminum alloy liquid, and after the scandium is completely melted, the aluminum alloy liquid is subjected to slag removal and degassing refining. After that, the processed aluminum alloy liquid is subjected to press and die casting under the condition of a pressure of 88 MPa to obtain needle bar crankshaft rod blanks, needle bar column blanks and needle bar holding parts blanks. Then, the n...
Embodiment 3
[0040] According to the composition of Example 3 in Table 1 and its mass percentage, first add half of the aluminum ingot, heat it to 700°C to completely melt the aluminum ingot, then add silicon, copper and the remaining aluminum ingot, and wait until the silicon and copper are completely melted. Add nickel and zinc, adjust the temperature of the aluminum alloy liquid to 720℃, press into the magnesium flakes with a bell jar, after the magnesium is completely melted, stir the molten aluminum alloy liquid evenly, and let it stand for 10 minutes before slagging. Then, scandium is pressed into the aluminum alloy liquid, and after the scandium is completely melted, the aluminum alloy liquid is subjected to slag removal and degassing refining. After that, the processed aluminum alloy liquid was subjected to press die casting under the condition of a pressure of 86 MPa to obtain the needle bar crankshaft rod blank, the needle bar column blank and the needle bar holding part blank. Th...
PUM
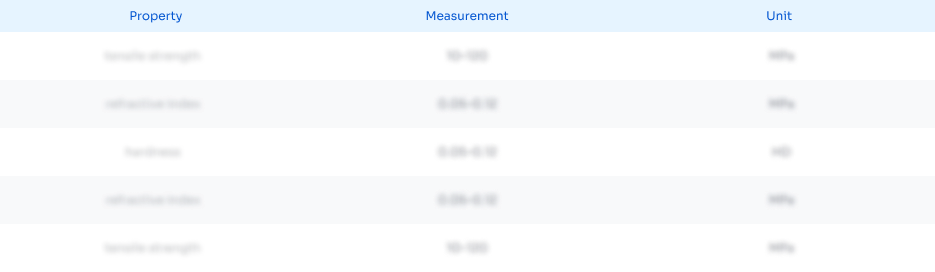
Abstract
Description
Claims
Application Information

- Generate Ideas
- Intellectual Property
- Life Sciences
- Materials
- Tech Scout
- Unparalleled Data Quality
- Higher Quality Content
- 60% Fewer Hallucinations
Browse by: Latest US Patents, China's latest patents, Technical Efficacy Thesaurus, Application Domain, Technology Topic, Popular Technical Reports.
© 2025 PatSnap. All rights reserved.Legal|Privacy policy|Modern Slavery Act Transparency Statement|Sitemap|About US| Contact US: help@patsnap.com