Continuous pressure sintering device and process for high-speed heavy-load brake pad
A technology of pressure sintering and brake pads, applied in lighting and heating equipment, furnace types, furnaces, etc., can solve the problems of basic structure and basic function stay, low energy utilization rate, low production efficiency, etc., to achieve improved labor conditions, The effect of high utilization rate of heat energy and high production efficiency
- Summary
- Abstract
- Description
- Claims
- Application Information
AI Technical Summary
Problems solved by technology
Method used
Image
Examples
preparation example Construction
[0043] A process for preparing high-speed heavy-duty brake pads using the device, specifically comprising the following steps:
[0044] Step 1: Start the upper computer to set the process parameters, open the horizontal boat feeding furnace door, place the loaded boat on the pallet plate of the propulsion cylinder, close the horizontal boat feeding furnace door, and the upper computer controls the propulsion cylinder to push the boat into the In the preheating section B, at the same time, a reducing atmosphere is introduced into the superalloy furnace tube through the gas supply device; wherein, the speed of pushing the boat of the propulsion cylinder is 1 boat / 60 minutes; that is, one boat is pushed every 60 minutes for continuous operation;
[0045] Step 2: The boat enters the preheating section B and heats up to 1050°C through the heating furnace. After holding the heat for 60 minutes, open the door of the horizontal boat feeding furnace, place the second boat on the pallet ...
Embodiment 1
[0050] Prepare a continuous pressure sintering device and supporting production process with an annual output of 170,000 sets (G-300 type) of railway high-speed train brake pads.
[0051] (I) User's technical parameter requirements (according to user requirements):
[0052] (Ⅰ-a) Brake pad size and weight:
[0053] The friction layer is 10mm thick, 40mm wide and 60mm long. Every 5 friction layers are sintered with the same steel backing substrate. The total area under pressure of the friction layer is 120cm 2 . The weight of each preformed blank is W 0 =184.8g. Steel back substrate size (provided by the user) is 5mm thick x 80mm wide x 294mm long, and weighs 917 grams per piece.
[0054] (I-b) Yield requirements.
[0055] 300 days (working days) per year, with an annual output of 170,000 sets / 300 days (Note: Each set of brake pads is composed of 5 friction plates welded together on a steel-backed substrate to form a set).
[0056] 1 The design of the main components of...
PUM
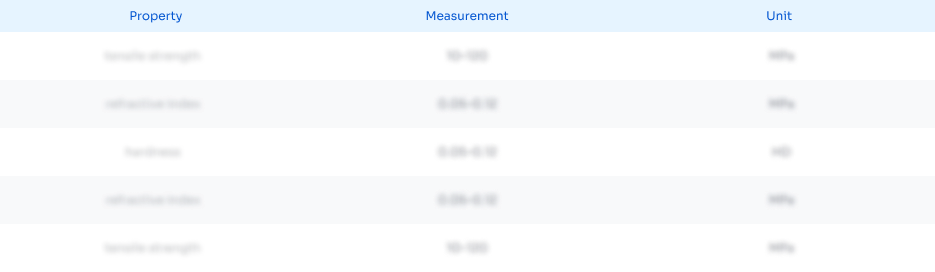
Abstract
Description
Claims
Application Information

- R&D
- Intellectual Property
- Life Sciences
- Materials
- Tech Scout
- Unparalleled Data Quality
- Higher Quality Content
- 60% Fewer Hallucinations
Browse by: Latest US Patents, China's latest patents, Technical Efficacy Thesaurus, Application Domain, Technology Topic, Popular Technical Reports.
© 2025 PatSnap. All rights reserved.Legal|Privacy policy|Modern Slavery Act Transparency Statement|Sitemap|About US| Contact US: help@patsnap.com