Engine balancer
A technology of balancing device and engine, applied in the direction of transmission, gear transmission, hoisting device, etc., can solve the problems of reduced gear assembly accuracy, difficulty in maintaining backlash accuracy, and difficulty in application.
- Summary
- Abstract
- Description
- Claims
- Application Information
AI Technical Summary
Problems solved by technology
Method used
Image
Examples
Embodiment 1
[0029] In this embodiment, a description will be given of a device structure that includes a transmission gear for transmitting power in addition to a gear for synchronizing counterweights.
[0030] figure 1 It is an example of the structural diagram of the balancing device of this embodiment. The balancer 50 is mounted on the bottom of an unshown engine block, and transmits power derived from a not-shown crankshaft to the input gear 16 provided coaxially with the input shaft 17 . On the other hand, in the balancing device 50, the driving shaft 1 is fitted with the driving gear 3 and is rotatably supported by the driving gear bearings 5a, 5b, and the driven shaft 2 is fitted with the driven gear 4 and is rotatably supported by the driven gear bearing 6a. , 6b is rotatably supported, and the driving shaft counterweight 13 and the driven shaft counterweight 14 are arranged at positions deviated from the rotation center on each shaft, and the driving gear 3 and the driven gear 4...
Embodiment 2
[0037] Figure 5 This is an example of a block diagram of the engine balancer when the transmission gear of the present embodiment is omitted. The input gear 16 is directly meshed with the drive gear 3, the drive shaft 1 and the sleeve 7, and the sleeve 7 and the drive gear 3 are pressed in, and the fixed pin 9 is firmly pressed into the flange 12 integrally formed on the drive shaft 1, and The aperture that is provided with on the driving gear 3, prevents the separation of the two. Since other structures and functions are the same as those in Embodiment 1, descriptions thereof are omitted. By adopting such a structure, one gear can be omitted, and not only an inexpensive system can be configured, but also the size of the body can be reduced.
PUM
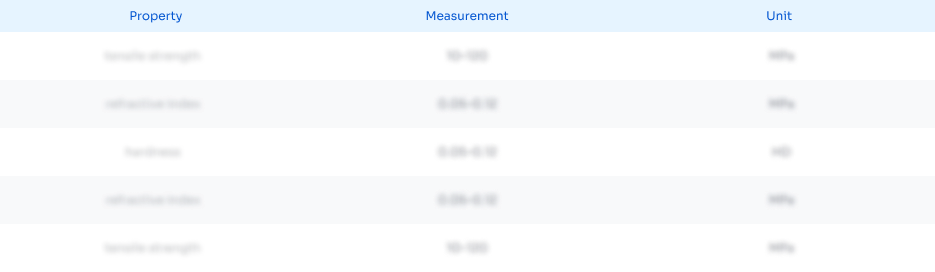
Abstract
Description
Claims
Application Information

- R&D
- Intellectual Property
- Life Sciences
- Materials
- Tech Scout
- Unparalleled Data Quality
- Higher Quality Content
- 60% Fewer Hallucinations
Browse by: Latest US Patents, China's latest patents, Technical Efficacy Thesaurus, Application Domain, Technology Topic, Popular Technical Reports.
© 2025 PatSnap. All rights reserved.Legal|Privacy policy|Modern Slavery Act Transparency Statement|Sitemap|About US| Contact US: help@patsnap.com