Yak wool loose fiber supercritical carbon dioxide dyeing process method
A technology of carbon dioxide and process method, which is applied in the field of textile printing and dyeing, can solve the problem of no loose fibers of yak cashmere, and achieve the effect of good dyeing quality, low overall cost and short dyeing process
- Summary
- Abstract
- Description
- Claims
- Application Information
AI Technical Summary
Problems solved by technology
Method used
Image
Examples
Embodiment 1
[0010] Example 1: First, put a certain amount of disperse dye in the dye kettle, and put the decolorized yak wool loose fiber into the dye kettle at the same time, and then open valve B (2) and valve C (3), Close valve A (1) and valve D (5), carbon dioxide flows out from the carbon dioxide storage tank through the heat exchanger, dye kettle, and enters the dyeing kettle. The carbon dioxide in the dye kettle and dyeing kettle system is pressurized to 7.3Mpa, and the carbon dioxide is in a supercritical state At this time, turn on the carbon dioxide circulation pump (4), heat the dyeing kettle to 90°C, the pressure is 24MPa, the time is 60min, open valve A (1), valve D (5), close valve C (3) and carbon dioxide circulation pump (4) , use the separation kettle to separate the dye in the carbon dioxide, the dye enters the dye kettle, the carbon dioxide enters the carbon dioxide storage tank through the carbon dioxide cooling system, separates for 20 minutes, the dyeing kettle is...
Embodiment 2
[0011] Example 2: First, put a certain amount of reactive disperse dye in the dye kettle, and put the decolorized yak wool loose fiber into the dye kettle at the same time, and then open valve B (2) and valve C (3) , close valve A (1) and valve D (5), carbon dioxide flows out from the carbon dioxide storage tank through the heat exchanger, the dye kettle, and enters the dyeing kettle. The carbon dioxide in the dye kettle and dyeing kettle system is pressurized to 7.3Mpa, and the carbon dioxide is supercritical. state, turn on the carbon dioxide circulation pump (4), heat the dyeing kettle to 120°C, the pressure is 28MPa, and the time is 45min, open valve A (1), valve D (5), close valve C (3) and carbon dioxide circulation pump (4 ), use the separation kettle to separate the dyes in the carbon dioxide, the dye enters the dye kettle, the carbon dioxide enters the carbon dioxide storage tank through the carbon dioxide cooling system, separates for 30 minutes, the dyeing kettle is ...
Embodiment 3
[0012] Example 3: First, put a certain amount of reactive disperse dyes in the dye kettle, and put the decolorized yak wool loose fibers into the dye kettle at the same time, and then open valve B (2) and valve C (3) , close valve A (1) and valve D (5), carbon dioxide flows out from the carbon dioxide storage tank through the heat exchanger, the dye kettle, and enters the dyeing kettle. The carbon dioxide in the dye kettle and dyeing kettle system is pressurized to 7.3Mpa, and the carbon dioxide is supercritical. state, turn on the carbon dioxide circulation pump (4), heat the dyeing kettle to 110°C, pressure 26MPa, time 50min, open valve A (1), valve D (5), close valve C (3) and carbon dioxide circulation pump (4 ), the dye in the carbon dioxide is separated by the separation tank, the dye enters the dye tank, the carbon dioxide enters the carbon dioxide storage tank through the carbon dioxide cooling system, and is separated for 25 minutes. The dyeing tank is depressurized, a...
PUM
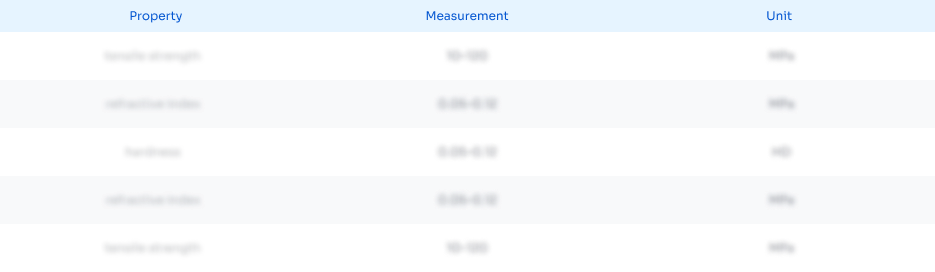
Abstract
Description
Claims
Application Information

- R&D Engineer
- R&D Manager
- IP Professional
- Industry Leading Data Capabilities
- Powerful AI technology
- Patent DNA Extraction
Browse by: Latest US Patents, China's latest patents, Technical Efficacy Thesaurus, Application Domain, Technology Topic, Popular Technical Reports.
© 2024 PatSnap. All rights reserved.Legal|Privacy policy|Modern Slavery Act Transparency Statement|Sitemap|About US| Contact US: help@patsnap.com