Low-temperature control process for oven baking of annular sleeve kiln
A technology of annular sleeve and oven, applied in the field of temperature control of annular sleeve kiln, can solve difficult temperature control requirements and other problems, achieve the effects of reducing control difficulty, easy implementation, and guaranteed baking quality
- Summary
- Abstract
- Description
- Claims
- Application Information
AI Technical Summary
Problems solved by technology
Method used
Image
Examples
Embodiment 1
[0020] Concrete operating method of the present invention comprises the steps:
[0021] (1) Turn on the cooling fan, high temperature fan, drive fan and other equipment, and the combustion chamber has the ignition conditions;
[0022] (2), the discharge speed is controlled at 90 seconds;
[0023] (3) Adjust the driving air pressure to 12-15kpa, adjust the high-temperature fan speed, control the negative pressure of the lower combustion chamber at about -100~-50pa, and control the lime cooling air volume at 4800-5200m / h;
[0024] (4) Control the individual air volume of the lower burner at 140-160 m / h, open the gas valve, manually adjust the gas flow after the burner is ignited successfully, and control the flame to the minimum, so that no flame can be seen from the observation hole of the burner panel, and only faint light can be seen as the standard;
[0025] (5) Observe the rise of the lower combustion chamber, and always keep the negative pressure of the lower combus...
Embodiment 2
[0028] The rest of the steps are the same as in Example 1, the difference lies in the temperature rise method in the low temperature zone of the lower combustion chamber. If the adjustment accuracy cannot be achieved on site, the gas volume can be increased by adjusting the gas manual valve and the temperature rise gradient can be reduced by increasing the lime cooling air volume. To achieve, the lime cooling air volume should not exceed 7000m3 / h.
[0029] The low-temperature control process of the annular sleeve kiln oven of the present invention effectively meets the current domestic sleeve kiln’s temperature requirements for refractory baking when the oven is put into operation, and makes up for the fact that the oven control method provided by the foreign party cannot match the domestic refractory baking temperature. Requirements to match the drawbacks. The control of key parameters by this process control method avoids the phenomenon of large temperature fluctuations caus...
PUM
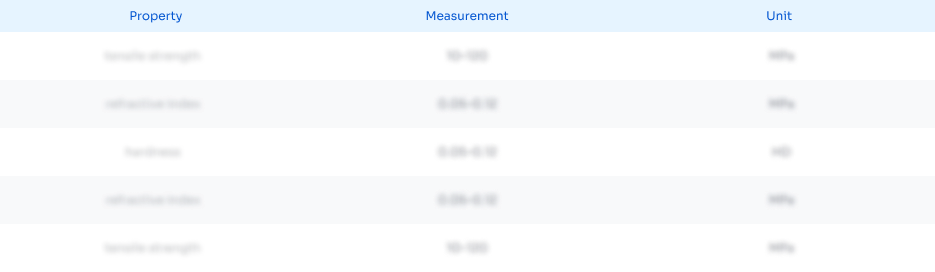
Abstract
Description
Claims
Application Information

- R&D
- Intellectual Property
- Life Sciences
- Materials
- Tech Scout
- Unparalleled Data Quality
- Higher Quality Content
- 60% Fewer Hallucinations
Browse by: Latest US Patents, China's latest patents, Technical Efficacy Thesaurus, Application Domain, Technology Topic, Popular Technical Reports.
© 2025 PatSnap. All rights reserved.Legal|Privacy policy|Modern Slavery Act Transparency Statement|Sitemap|About US| Contact US: help@patsnap.com